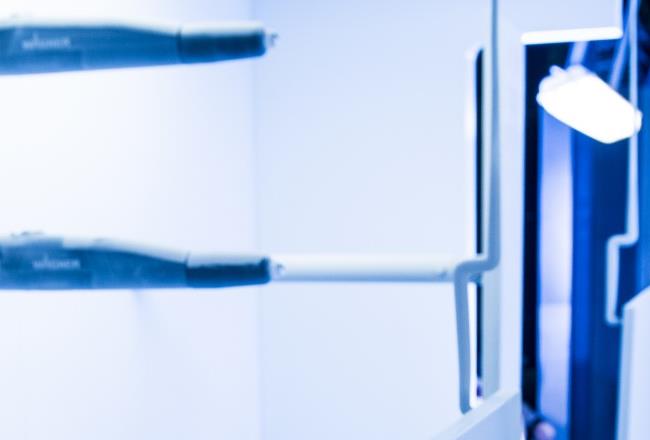
Bringing the benefits of powder coating to heat-sensitive substrates
Powder coating has many benefits – but traditionally, it’s been difficult to powder-coat MDF and similar engineered woods. That’s because the powder needed to be cured at temperatures over 150°C, which made boards more likely to crack, bubble and pop.
Technologies like Covestro’s Uralac® Ultra, Uralac® Engain, and Uralac® UV provide solutions. Because they can be cured at temperatures as low as 120°C, or even lower for Uralac® UV, they make it much easier to coat engineered wood. These technologies can bring all the following benefits of powder coating to heat-sensitive substrates (HSS):
Design freedom
Open imaginative possibilities
Uralac® Ultra and UV’s unique single-layer coating process requires just one sanding application, and a curing temperature as low as 120°C.
This means you can produce a solid, seamless powder coating finish up to 10 times faster than with waterborne equivalents. And, unlike with traditional UV-cured roller coatings, you can also coat complex designs and shapes, including hollows, contours and edges.
In short, by swapping liquid-coated MDF for a powder coating based on Uralac® Ultra, Engain, or UV, you can create more innovative, imaginative products that bring you a competitive advantage.
Durable
Made for tough environments
The advanced binding technology of Uralac® solutions for HSS can bring a new level of durability and protection to powder coatings. Thanks to their strong polyester-urethane binder, these resins have excellent resistance to wear and tear from scratches, abrasion, and UV – enabling a flexible finish with minimal yellowing or peeling.
Uralac® solutions for HSS have passed a range of industry tests for durability, including NEN-EN 12720, Blue Wool Scale, and hinge hole (Ledro test) benchmarking.
Economical
Saves time and resources
Thanks to their low curing temperatures and unique all-sides-in-one-pass coating process, Uralac®-based coatings for HSS require less water, energy, and time to produce than liquid coatings. Removing the sanding step between layers enables further time and material savings. And, since the powder overspray is almost 100% recyclable, there is also less waste.
As a result, customers using Uralac®-based systems for HSS have been able to produce coatings up to 10 times faster, and reduce their costs by up to 45%, compared to when using liquid coatings. Uralac®-based powders for HSS can even enable cost savings during storage and transportation, thanks to the absence of solvents and their 100%-solid content.