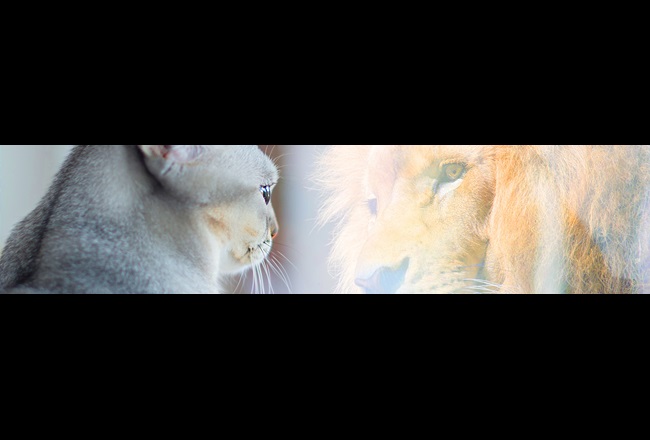
Customizing cast PU elastomers for demanding applications
Cast PU is durable and flexible. Now it can be engineered for demanding new applications
Durability, flexibility, a high compression set and chemical resistance make cast polyurethane (PU) a logical material choice for many hard-wearing industrial applications. Rollers on production lines and wheels on forklifts all benefit from the smooth movement, high load bearing and chemical resistance that cast PU elastomers are known for. Items like mining screens and piping inspection discs also rely on this type of material because it is so highly resistant to everyday use and impacts.
However, in some environments, conventional cast PU is limited by its inherent chemical nature. Some railway and mining applications demand fire-resistant materials, and this flame retardancy must often go hand-in-hand with antistatic performance. Locations in high humidity areas typically need antibacterial materials, and parts that are immersed in water must resist the process of hydrolysis.
We can customize cast PU to handle the specific requirements for a wide range of cutting-edge applications. Explore several examples below.
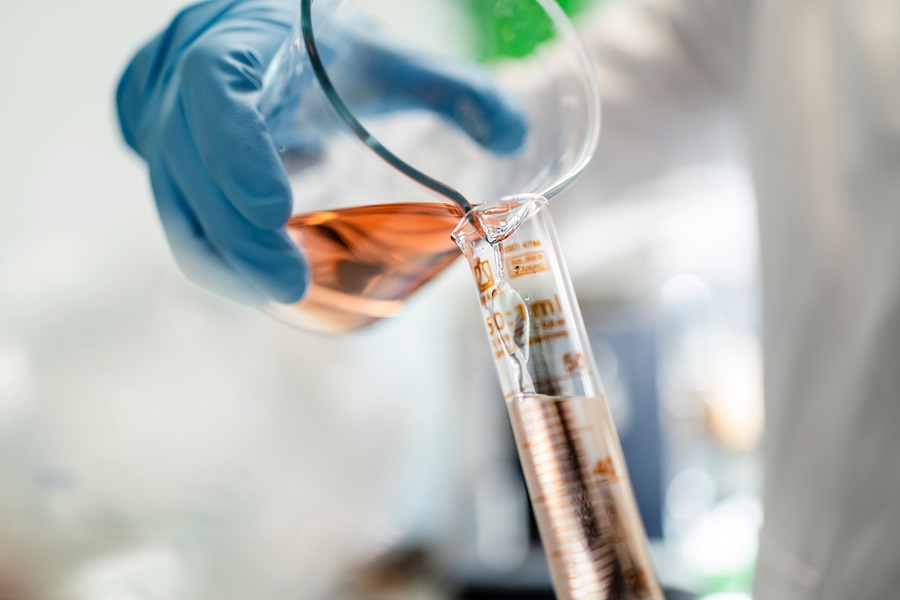
Example: antibacterial materials for cast PU parts in mining
In warm or wet surroundings, the ester-based PU scrapers and screens used in mines and quarries can develop fungi and microbes, destroying a part that normally lasts several years in just a few months. Since biocidal mercury-based catalysts are no longer used, we offer solutions that enable cast polyurethane parts to resist microorganisms effectively, avoiding premature degradation. Our antibacterial materials provide these properties without sacrificing the inherent qualities of PU.
Example: hydrolysis protection for immersed PU parts
Water can actually break down the chemical bonds in ester-based PU chains in just a few weeks, causing elastomer parts to deform, especially if the parts remain immersed at high temperatures of 60°C or more. We offer multiple material solutions that slow down the hydrolysis process, which makes them interesting for offshore subsea applications such as cable protection systems or for mining parts such as scrapers and flotation cells.
Example: enhanced abrasion resistance for tough mining environments
At mines and quarries, PU screens are often used to sort heavy and sharp rocks. Chips and knicks can destroy the parts over the course of years or even just months depending on the conditions – despite the fact they are made with inherently durable materials. Here, our additive solutions can reduce abrasion significantly, extending the already impressive lifetime of cast PU parts.
Example: antistatic materials for wheels and roller applications in printing and agriculture
Most plastics act as natural insulators. Like natural rubber, cast PU is not conductive. However, when PU rollers are used in printing or in agriculture, an electric charge can form on the surface, triggering an electrostatic discharge (ESD) with sparks. If solvents or fuel are present, this brings the real danger of fire or explosion. We offer additives that yield antistatic materials and ESD materials that actually dissipate this electrostatic build-up, yielding a PU-based alternative to low resistivity materials while improving safety at work.
Example: fireproof parts for the electronics and rail sectors
Polymer parts are widely used in electronics and in the rail sector. We offer a selection of halogen-free solutions that allow us to achieve several standards for fire-resistant materials including UL94-V0 and AS1334.
Components that are highly resistant to fire often require synergy with electrical resistivity, avoiding sparks on one side of a part while ensuring that the PU is fireproof on the other. Our innovative fire-resistant materials can deliver exactly this combination.
Example: UV-stable materials for infrastructure with high sunlight exposure
Cast polyurethane is a long-time choice for bollards and infrastructure items subject to high wear and fatigue. However, extended exposure to sunlight and ultraviolet radiation can change the molecular structure of PU. We have developed solutions that enable UV stability and prevent photodegradation as well as material failure.
Durability makes cast PU a popular choice, but traditionally it lacks specific properties required for some demanding applications. So we’ve created solutions that enable it to stand up to hydrolysis and microbes, enhance its abrasion resistance, reduce electrostatic build-up and make it fireproof.
Key benefits
- Customizable: Cast PU can be fine-tuned to meet application requirements consistently.
- Tough and durable: Cast polyurethane is a top choice for tough wheels, rollers and high-use parts.
- Safe and compliant: Fire resistance and anti-microbial additives meet safety & regulatory standards.
- Fireproof: Although polymers are flammable, our solutions make cast PU flame retardant.
- Easy to process: Most of our additives can be added to chemical PU mixtures by hand or machine.