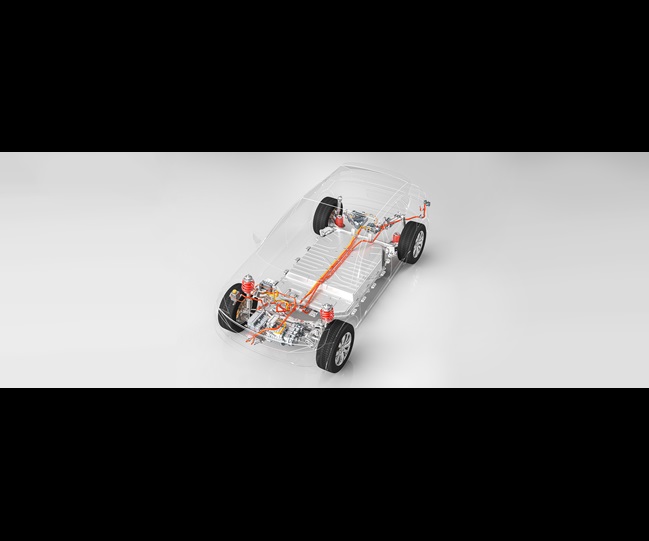
Polycarbonate solutions support the electrification trend in mobility
Polycarbonates open up new possibilities for powertrains
Up until now, automotive manufacturers have mainly used semi-crystalline materials in conventional combustion engines. The increasing electrification trend in the automotive industry will lead to new requirements which could be solved in a different way than in the past. This applies to parts like inverters, converters, onboard chargers, HV connectors, charging interfaces, junction boxes, power distributors, onboard-chargers, sensors and control units. Cooling and thermal management devices as well as crash absorbers also need to be ready for mass production.
Polycarbonate materials meet tough technical requirements
“Polycarbonates have long been a key material in the EE and automotive industry, and will continue to offer new answers for electric powertrain companies and OEMs when it comes to the challenges of dimensional stability and mass production.”
Key Benefits
- Dimensional stability Nearly isotropic molding shrinkage of 0.7/0.75 %
- High heat resistance Constant properties over a wide temperature range, even without glass fibers.
- Flame-retardancy Category V-0 of Underwriters Laboratories' UL94 flammability classification.
- Toughness IZOD ISO180A, 23 °C, 3.2 mm, 60-90 kJ/m²
- Great sensor transparency Sensor transparency for LiDAR and RADAR frequencies, from visible to 5G frequencies
- Convincing electrical properties Polycarbonate material properties offer excellent possibilities for the EE&A industry