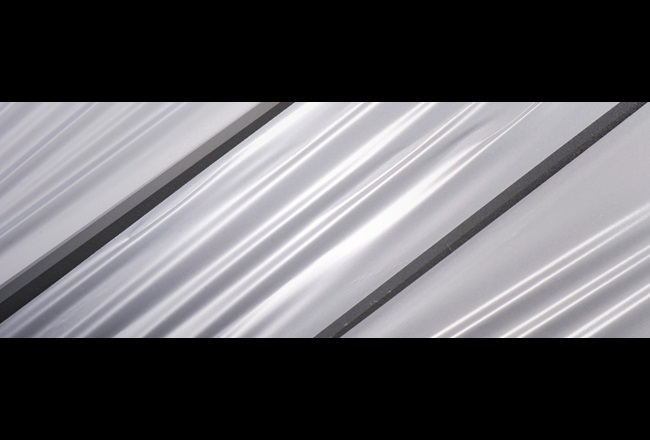
Processing technology
Welding: Mulitple methods for different materials
There are a number of ways in which polycarbonate and thermoplastic polyurethane films can be effectively joined. These include ultrasonic welding, heat sealing, high frequency welding, laser welding and impulse welding. Choosing the right method requires considering the materials to be joined and the intended application.
Five key methods are available for joining PC and TPU films:
1. Ultrasonic welding uses vibrations produced by a generator to create friction, which quickly heats the film. Heat in combination with pressure makes it possible to join films.
2. Heat sealing, or hot platen sealing, joins Dureflex® and Platilon® film or composite laminates by heating areas already under pressure until fusion occurs.
3. High frequency (HF) welding or dielectric sealing uses a rapidly alternating, high-energy electromagnetic field to stimulate the molecules of two overlapping layers of laminate, causing the two layers to fuse at the point of contact.
4. In the case of laser welding, the transparent upper film permits the transmission of the laser wavelength and the lower film absorbs the laser waves. This softens the lower film and passes the heat on to the upper film. Pressure is then applied to join the films.
5. Impulse welding joins our Dureflex® and Platilon® films by means of an insulated band heater. In contrast to the heat sealing process mentioned above, the welding tool is only heated for the duration of the welding process. Five key methods are available for joining PC and TPU films:
1. Ultrasonic welding uses vibrations produced by a generator to create friction, which quickly heats the film. Heat in combination with pressure makes it possible to join films.
2. Heat sealing, or hot platen sealing, joins Dureflex® and Platilon® film or composite laminates by heating areas already under pressure until fusion occurs.
3. High frequency (HF) welding or dielectric sealing uses a rapidly alternating, high-energy electromagnetic field to stimulate the molecules of two overlapping layers of laminate, causing the two layers to fuse at the point of contact.
4. In the case of laser welding, the transparent upper film permits the transmission of the laser wavelength and the lower film absorbs the laser waves. This softens the lower film and passes the heat on to the upper film. Pressure is then applied to join the films.
5. Impulse welding joins our Dureflex® and Platilon® films by means of an insulated band heater. In contrast to the heat sealing process mentioned above, the welding tool is only heated for the duration of the welding process. Five key methods are available for joining PC and TPU films:
Ultrasonic welding: For PC and TPU films
This method uses a sonotrode to transfer vibrations from a generator to the film to be welded and introduce vibrations into the weld seam. These vibrations are then converted into friction, which quickly heats the film. Pressure exerted by the sonotrode is used to simultaneously join and cool the seam. Applications which are compatible with the ultrasonic welding of Makrofol® DE film include medical packaging, visors, and protective housings. For Dureflex® and Platilon® films, ultrasonic welding may be applied to cut and weld parts like gloves and tubes, or to weld bags with custom-shaped seams.
Heat sealing (or hot platen): For TPU films
Heat sealing, or hot platen sealing, can be used to join our Dureflex® and Platilon® films, or composite laminates, by heating areas under pressure until fusion occurs.
Applications where Dureflex® and Platilon® film may be heat-sealed include bags, mattresses, appliques (e.g. letters and numbers) on uniforms and clothing, prosthetic sheathes, and flexible/reinforced industrial tubing.
Applications where Dureflex® and Platilon® film may be heat-sealed include bags, mattresses, appliques (e.g. letters and numbers) on uniforms and clothing, prosthetic sheathes, and flexible/reinforced industrial tubing.
High frequency (HF) welding: For TPU films
High frequency (HF) welding or dielectric sealing uses a rapidly alternating, high-energy electromagnetic field to stimulate the molecules of two overlapping layers of standalone or laminate constructions. The stimulated molecules create localized heat, causing the two layers to fuse together at the point of contact and create a weld. After cooling, the bond is as strong as the original materials. Applications where Dureflex® and Platilon® film may be high frequency welded or dielectrically sealed include protective clothing, shoe components, gel- and foam-filled cushions, surgical pouches, bellows, lumbar supports, hydration reservoirs, inflatable boats, and medical and commercial mattresses.
Laser welding: For TPU films
For laser welding, the most common transmission process, the upper film must be transparent to allow for the transmission of the laser wavelength – and the lower film must be able to absorb the laser waves. The lower film softens and transfers heat to the upper film. Suitable pressure applied to the weld then joins the films.
Laser welding is among the most rapid techniques used for continuous welding. Applications where Dureflex® and Platilon® film may be laser welded include the cutting and welding of parts such as gloves or tubing or welding bags with custom-shaped seams.
Laser welding is among the most rapid techniques used for continuous welding. Applications where Dureflex® and Platilon® film may be laser welded include the cutting and welding of parts such as gloves or tubing or welding bags with custom-shaped seams.
Impulse welding: For TPU films
Impulse welding joins Dureflex® and Platilon® films by means of an insulated band heater through which electricity flows for a brief period. In contrast to heat sealing, the welding tool in this process is only heated for the duration of the welding process. Applications where Dureflex® and Platilon® film may be impulse welded include medical bags and sealing seams.