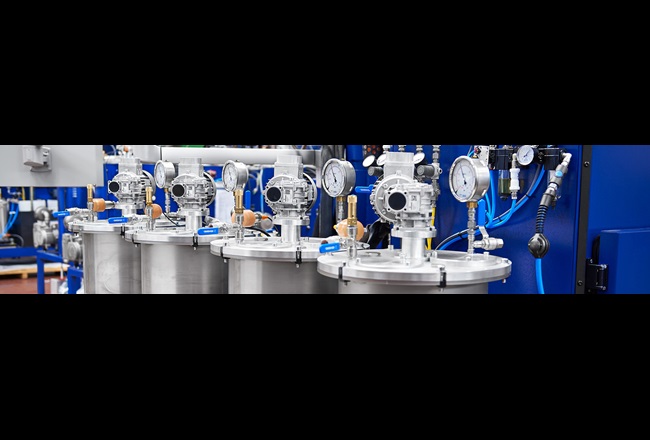
Improve casting machine productivity with peripherals and options
Peripherals to develop cast PU parts production
In order to support a continuous production, we provide peripherals which enable the feeding of the machinery whenever required. They make the machines capable to run continuously even large quantities of material thanks to the automatic feeding of the raw materials.
Continuous Disc Degasser
Hundreds of degassers are daily used over the world and its reliability is well known. This equipment enables continuous feeding of the machine with degassed material. It is fully adaptable to any Baulé® machine and avoids production stoppage during material preparation. Furthermore, it automatically delivers required amounts of material and minimizes heat degradation while there is no material stagnation.
Amine feeding devices
Covestro developed specific devices for a safer processing of amines. It is composed of a feeding system and a melting device.
The feeding device consists on a Glove box that secures all critical working and maintenance operations. It allows the operator to open the amine pellets drums and pour the granules into a hopper without any direct contact between the product and the operator, avoiding the exposure to the amines dust. Thanks to an high thermal efficiency coil, the melting device is able to melt several kind of amines at the lowest and uniform melting temperature and to deliver a continuous output of material.
Granules processing unit
Covestro has developed an equipment which allows processing of granular materials (polymers solid fillers such as rubber, TPU, cast PU or else) coming from worn parts (recycling of used parts) or from production waste (non-saleable parts or casting scraps). After reducing these parts into granules, they can be reused and integrated into new cast PU parts thanks to the Baulé® granules processing unit.
This equipment is developed for the mixing and metering of these granules into PU parts production. Upstream work is to incorporate the fillers into the chosen material (usually a polyol), then the materials are thoroughly blended in order to obtain a homogeneous mixture. Once degassed, the blend is ready to be processed through a special metering device.
Automated processing unit
In response to requests for automatic casting process and consistency expectations, Covestro is able to implement automated units. Thanks to a dedicated and intuitive program on the machine HMI, it is possible to set, control and record movements of peripherals such as robot according to the production requirements:
- Cartesian robot
- Turntable
- Conveyor equipment
Rotational casting
Rotational Casting is a processing technique which eliminates the costs associated with the moulds and ovens by casting PU mixture directly on a rotating roll’s core. Thanks to that technique our customers can easily manage the casting of rolls with different diameters and increase their productivity while limiting their investment and reducing their loss of the material during the production.
Depending on the needs, the Rotational Casting equipment can vary from a very simple and basic dispensing machine integrating only few dedicated options to fit with this technology or can also be much more sophisticated and automated with precise integrated systems.
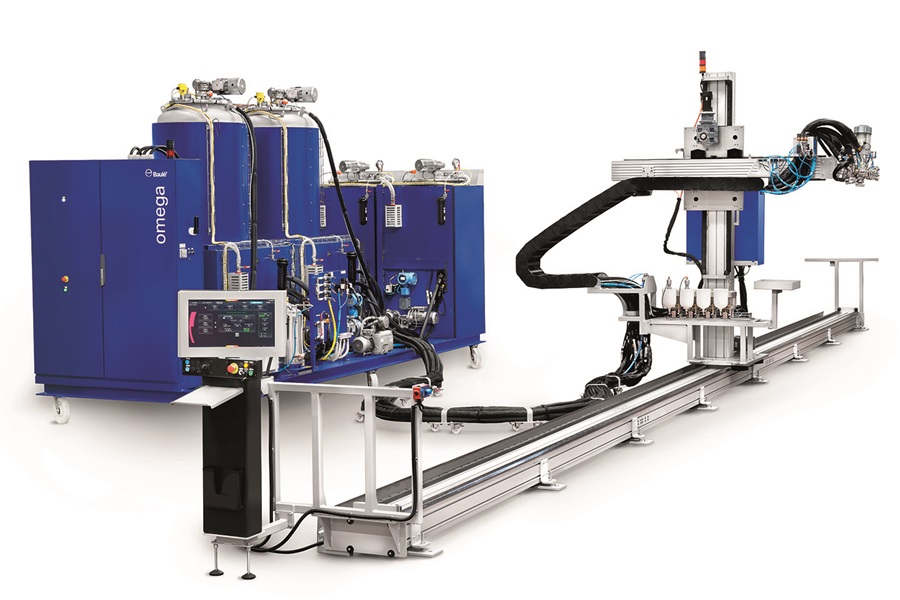
Options to boost the machines capabilities
Decades of activities and solutions building in the cast polyurethane field lead us to develop a comprehensive range of options for our machines. All together they are able to answer to any process requirements, often enlarging casting flexibility and production capacities.
Pigment, catalyst or additive injection
Our Baulé® Additive Injection Device enables injection of additives (pigments, catalysts, UV stabilizer…) directly in the mixing chamber. Covestro is an inventor and pioneer of mastering the crucial transitory phase at the first instant of the shot. Thanks to this feature, it is not necessary to pre-mix additives in the drum or in the machine tank before casting. It is very easy to adjust the additives ratios according to your needs or switch from one additive to another one in a few seconds.
Auto-calibration
Calibration is an essential step which, through accuracy, guarantees consistent and perfected production. As a manual process, it does require a daily investment of time, effort and precision. Although helpful and effective, this method requires an advanced mastery of the various steps in order to obtain accurate results.
The purpose of the auto-calibration is to have a step-by-step guided, error-free and highly accurate calibration method. Thanks to the connected scale and the dedicated software functions, the auto-calibration allows an automatic multi-point correction of the pump speed in order to get an accurate flowrate on the full output spectrum.
Low Exposure Oven
Thanks to a constant analysis and assessment, Covestro Elastomers came up with a solution to further perfect the design machine’ s ovens and ensure our users safety and well-being while handling chemical products.
Auto-calibration is an option that made this daily task much easier for our operators as they only have to supervise the action. On top of that, it improves accuracy because the machine automatically corrects any fluctuation, thus avoiding any human error.
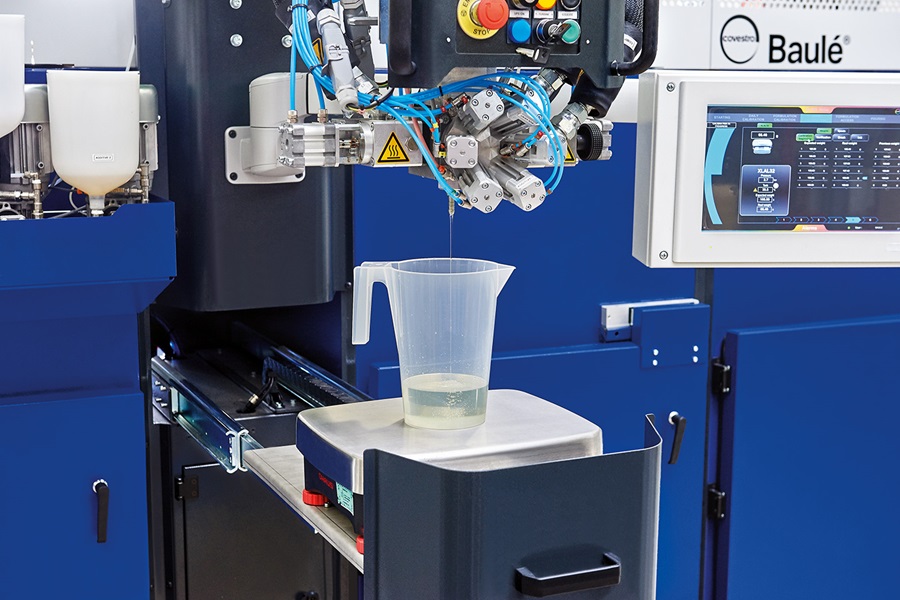