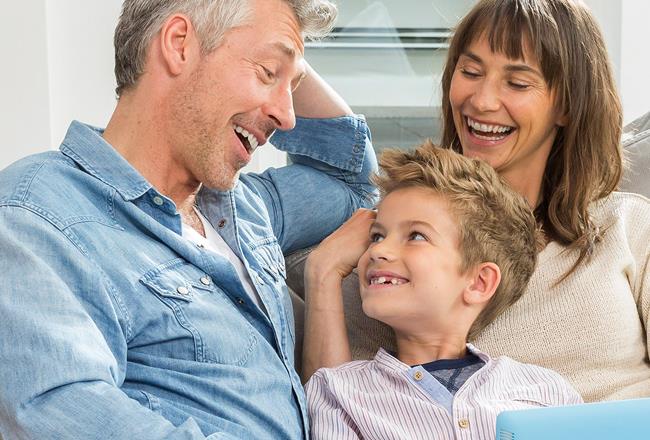
Top comfort and durability with more sustainable mattress foam
Creating a polyurethane foam mattress for comfort and a sustainable future.
When producing the raw materials for mattresses, a significant share of fossil resources is replaced at the beginning of the supply chain by renewable raw materials, for example from plant waste sources (bio-circular). These renewable resources have a much better sustainability profile and significantly reduce CO2 emissions. Another advantage is that manufacturers are less dependent on fossil resources and can offer a finished product, for example mattress foam, that has a lower impact on the environment and continues to offer the same high level of quality and durability.
Implemented in a wide range of industries, the mass balance methodology can also be applied, for instance, by manufacturers of mattress foam. In this approach, raw materials derived from biomass or waste are fed in at an early stage of raw material extraction and mathematically attributed to the finished products. This certified process by ISCC (International Sustainability and Carbon Certification) ensures complete transparency and traceability of the renewable resources throughout the entire production process.
For consumers, opting for such a mattress means actively contributing to reduce greenhouse emissions. Apart from a healthy sleep, consumers can feel confident that they are making a smart investment for both their own well-being and the planet's future. This is by no means a distant vision. Foamers and consumers can begin today itself and contribute to a more sustainable tomorrow.
Achieving climate goals with more sustainable raw materials.
A growing number of companies across the globe have to deal with the challenge of phasing out fossil-based raw materials with those that are more sustainable and have a significantly lower impact on the environment.
In this regard, mass balance is a major step forward. But, what is mass balance and how does it work?
The mass balance approach is a certified and widely used method to introduce more sustainable raw materials into complex production chains. In this method, fossil-based materials are replaced by renewable ones derived from e.g., bio-circular sources (e.g. plant residues or used cooking oils) in an early stage of raw material extraction and later attributed to the finished products. Manufacturers can use these materials in production without any need to change their formulations, equipment and processes. The potential is enormous and allows manufacturers to gradually transform their product portfolio towards a more sustainable one and achieve their climate goals.
Covestro manufactures the renewable-attributed raw materials, such as toluene diisocyanate (TDI) and polyether, in major production sites from all regions. The sites are certified according to the ISCC PLUS standard.
Joining forces with Sinomax and The Vita Group, pioneering partners for more sustainability.
Covestro produces more sustainable materials to benefit the environment and enable customers and partners to create more sustainable products like mattress foam. Our partnership with Sinomax and The Vita Group led to a new generation of polyurethane (PUR) foam made partially from our renewable-attributed TDI.
With Sinomax, a global manufacturer and distributor of polyurethane comfort products based in China, Covestro finalized its first commercial supply agreement. Both companies are committed to promoting the circular economy. Moreover, Sinomax aims to be the first customer to use renewable-attributed TDI to reduce its CO2 emissions in APAC.
Recognized by Interzum’s “High Product Quality” Award in 2023, OrbisTM Plus MB foam from The Vita Group is its latest innovation of flexible PUR foam made with raw materials sourced from renewable and recycled sources. TDI, being a vital component of this product, is produced by Covestro with ISCC PLUS-certified feedstock.
One of the major benefits of using ISCC PLUS-certified TDI: Sinomax and The Vita Group do not need to change any of their proven formulations, equipment and processes. And yet, Sinomax and The Vita Group are now in a position to gradually transform their portfolio to more sustainable products and, at the same time, achieve their climate goals.
“With our shift to more sustainable products, we are helping customers in various industries achieve their climate targets and drive the transition to a circular economy. At the same time, we are strengthening the use of alternative raw materials and reducing CO₂ emissions along various value chains.”
“CQ” – Covestro’s commitment to circularity
To underline our commitment to circularity, and to clearly identify how our products support our circular vision as well as the goals of our customers and partners towards sustainability, we have introduced “CQ”, a brand for our products aimed at driving circularity. The branding suffix “CQ” stands for circular intelligence. Together, C and Q underline how essential innovative solutions can drive circularity forward. Desmodur® CQ T80 and Desmodur® CQ T65 were among the first products available with a significantly reduced carbon footprint. The portfolio of products and grades has, of course, expanded in the meantime and Covestro continues to pursue its goal of making the range of solutions bearing the CQ mark grow constantly.
Key Benefits
- Sustainable: More sustainable foam significantly reduces CO₂ emissions, cradle to gate.
- Fast: Can be implemented directly without compromising on quality.
- Seamless: No need to alter proven formulations, equipment and processes.
- Adaptable: More sustainable TDI and polyether help companies meet their climate goals.