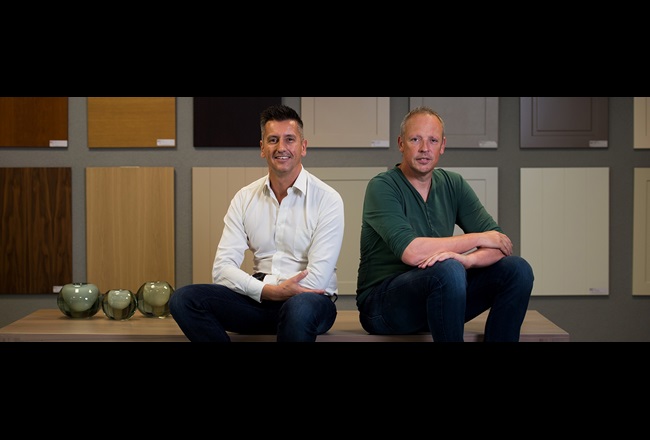
Ten times faster with powder coatings
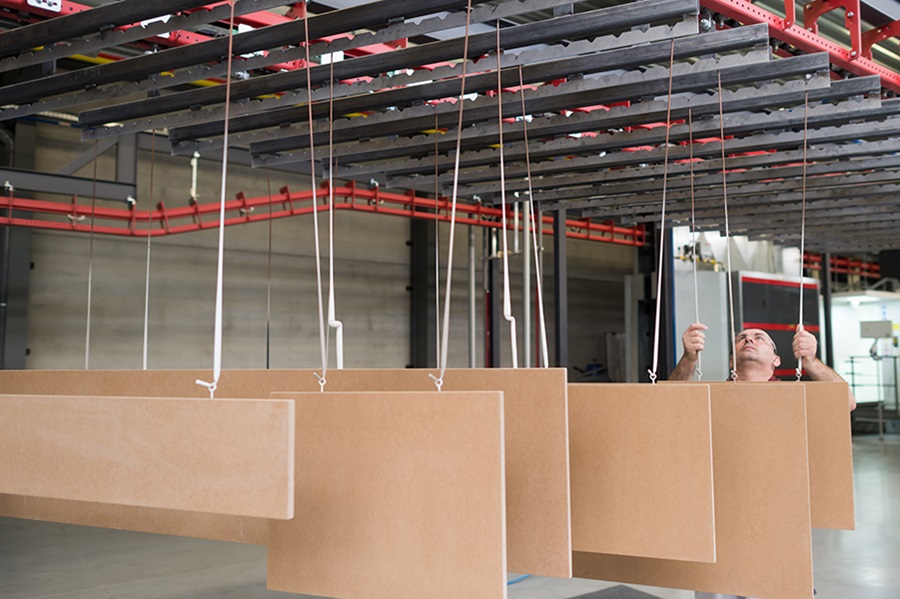
Why now?
Powder coatings are more scratch-resistant, more humidity-resistant, and offer good chemical resistance, while at the same time providing excellent surface appearance with a range of gloss levels.
"We also found that architects were particularly interested in the product's very low carbon footprint,'' says Laureyssen. "This characteristic helps architects achieve more 'green' credentials in their proposed tenders for local and national government new builds."
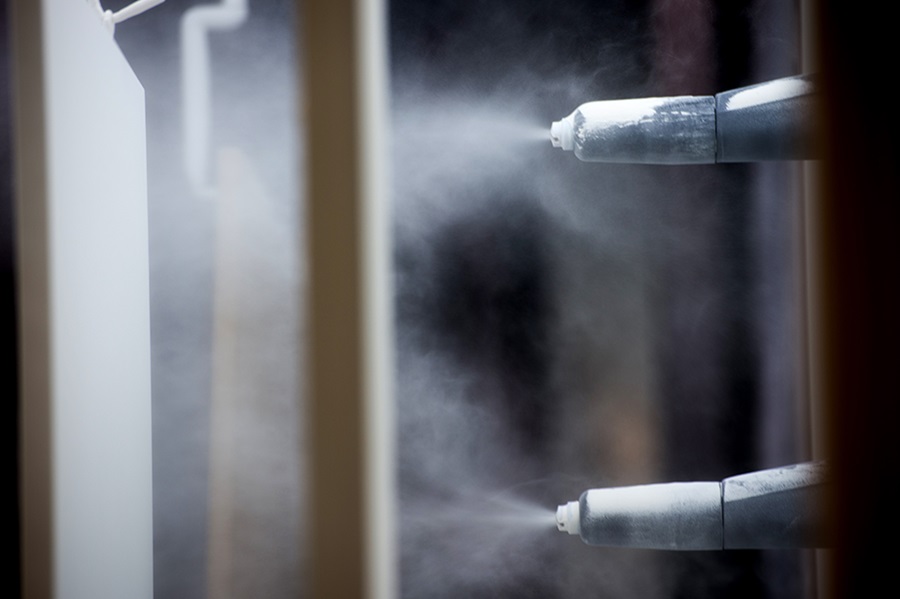
Why is powder coating so fast?
"Powder coatings are faster to process than liquid paint because there is no priming and less sanding involved," says Kempa owner Maeyninckx. "There's also a reduced curing time. So you can see why it is ten times faster – especially for single-coat processing. But make no mistake, this increased speed does not impact quality at all."
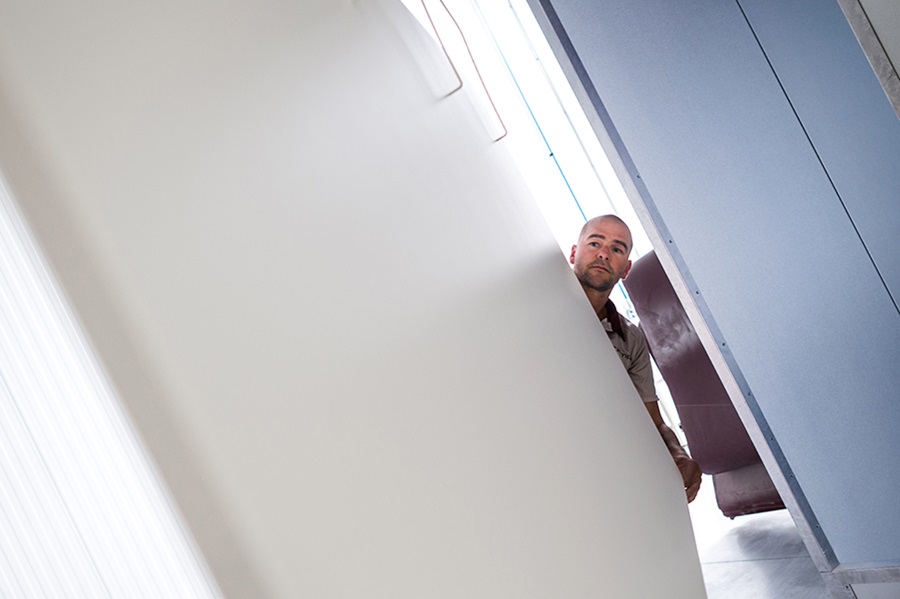
Frequently asked questions
How do we spray powder on standard 'non-conductive' MDF?
For application of the powder, moisture within the MDF is used for conductivity. A moisture content of 4-8% of total weight is sufficient to attract the powder.
Do we require special MDF for powder coating?
No special MDF is needed for powder coating – although there are differences between available qualities and types.
We advise evaluating the type of MDF you intend to use before making your products.
Further, we recommend a conditioned storage area to control the MDF's moisture content.
Is the oven I use for powder coating metal suitable for curing MDF too?
Most conventional curing ovens are convection ovens. Best results for MDF are reached with infrared radiation (IR) ovens.
With IR ovens, the MDF's surface can be heated quickly to cure the powder coating, while its core stays relatively cool.
With convection ovens, temperatures are often too high, or the MDF's core heats up too much because of the longer period needed to reach curing temperatures.