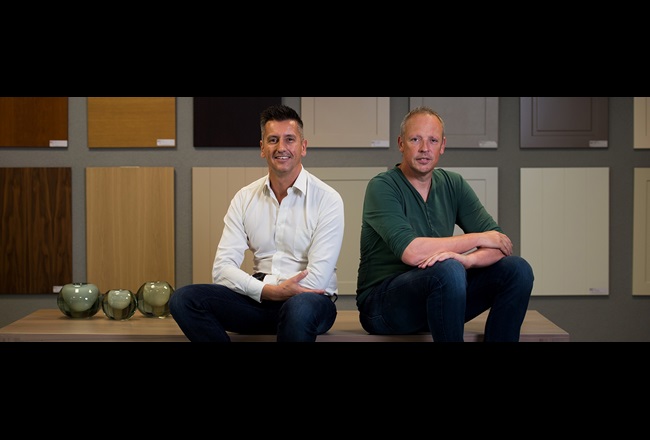
Zehnmal schneller mit Pulverbeschichtungen
Der Hersteller hatte zwar damit gerechnet, dass das Verfahren schneller sein würde, war jedoch überrascht, als das Team eine Verkürzung der Prozessdauer auf ein Zehntel erreichte. „Es hängt natürlich von der Art des Substrats und der Anzahl der Schichten ab“, räumt Firmeninhaber Paul Maeyninckx ein. „Aber mit dem Pulver ist eine Ofenzeit von nur drei Minuten ausreichend, während man mit Lack eine halbe Stunde benötigt.“
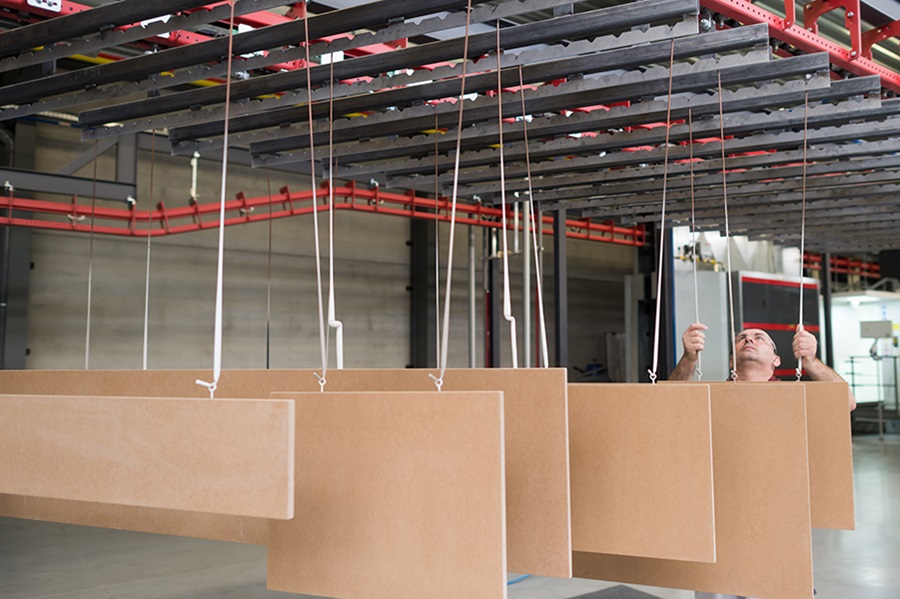
Warum gerade jetzt?
Die Pulverbeschichtungstechnologie ist bereits seit einigen Jahren verfügbar. Warum hat Kempa also bis jetzt mit der Einführung der Technologie gewartet? „Unsere Kunden sind spezialisierte Küchenbauer und sie sprechen uns bereits seit einigen Jahren immer wieder darauf an, ob wir auch Pulverbeschichtungen anbieten“, sagt Filip Laureyssen, Customer Care Manager bei Kempa.
„In den letzten drei Jahren hat das Interesse plötzlich stark zugenommen. Deshalb haben wir natürlich beschlossen, die Möglichkeiten zu prüfen. Außerdem waren wir der Meinung, dass die Technologie inzwischen so ausgereift ist, dass wir sie nutzen wollen.“
Der plötzliche Anstieg des Interesses an Pulverbeschichtungen beruht mit Sicherheit auf dem wachsenden Bewusstsein für die Vorteile. Die Küchenbauer hörten immer öfter von den Zeit- und Kosteneinsparungen im Vergleich zu Flüssiglacken sowie von der längeren Haltbarkeit.
Pulverbeschichtungen sind kratzfester, feuchtigkeitsbeständiger und bieten eine gute Chemikalienbeständigkeit. Gleichzeitig sorgen sie für ein hervorragendes Oberflächenbild mit verschiedenen Glanzgraden.
Wir haben auch festgestellt, dass Architekten besonders an der guten Ökobilanz des Produkts interessiert waren“, sagt Laureyssen. „Diese Eigenschaft hilft ihnen, bei ihren Ausschreibungen für Neubauten der lokalen und nationalen Behörden mehr ‚umweltfreundliche‘ Referenzen zu erhalten.“
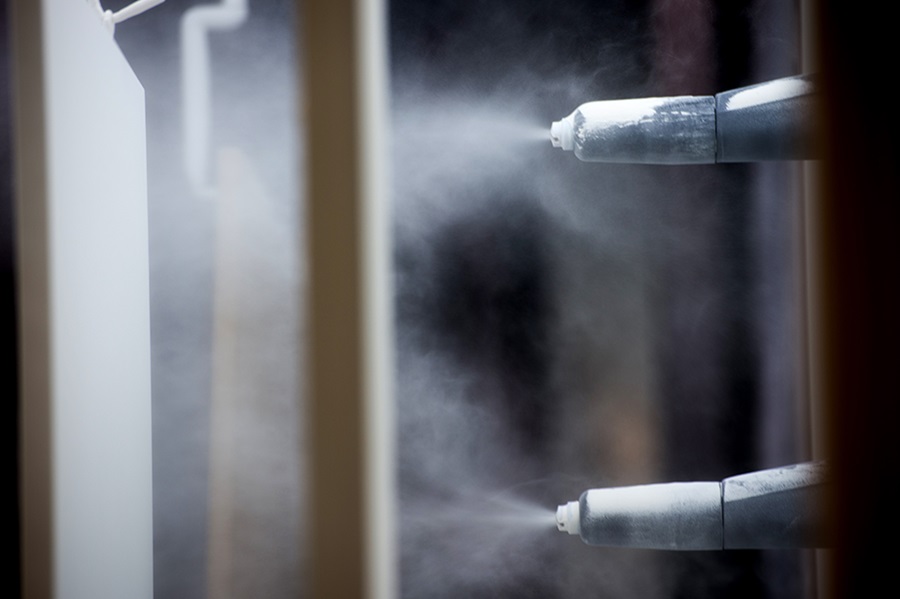
Warum geht Pulverbeschichten so schnell?
„Pulverbeschichtungen lassen sich schneller verarbeiten als Flüssiglacke, da keine Grundierung und weniger Schleifarbeiten erforderlich sind“, sagt Kempa-Inhaber Maeyninckx. „Außerdem ist die Aushärtungszeit kürzer. Das erklärt, warum das Verfahren zehnmal schneller ist – vor allem bei der Verarbeitung von Einzelschichten. Aber bitte nicht falsch verstehen: Die Qualität wird von dieser höheren Geschwindigkeit in keiner Weise beeinträchtigt.“
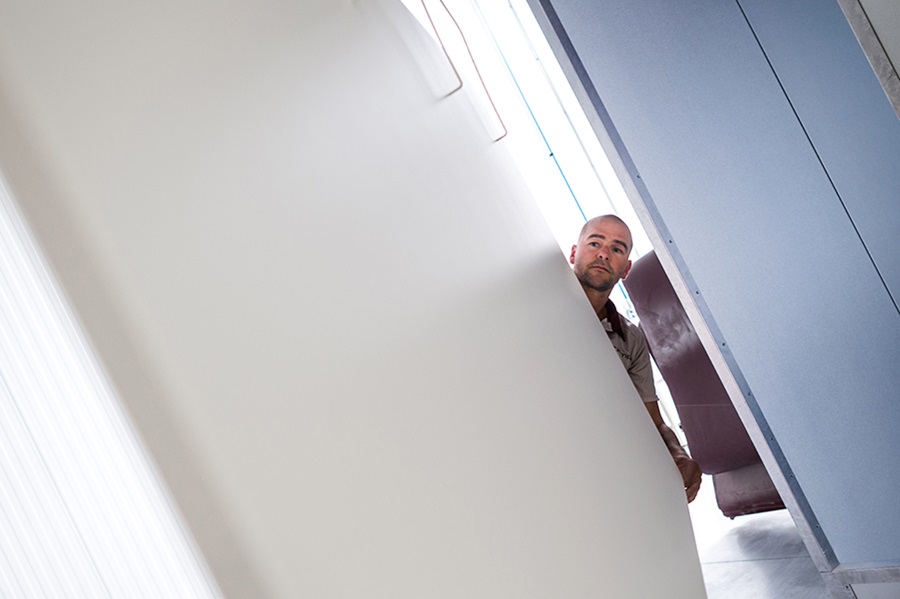
Häufig gestellte Fragen
Wie sprüht man Pulver auf „nicht leitende“ Standard-MDF-Platten?
Beim Auftragen des Pulvers wird die Feuchtigkeit in der MDF-Platte für die Leitfähigkeit genutzt. Ein Feuchtigkeitsgehalt von 4–8 % des Gesamtgewichts reicht aus, um das Pulver anzuziehen.
Benötigen wir spezielle MDF-Platten für die Pulverbeschichtung?
Für die Pulverbeschichtung sind keine speziellen MDF-Platten erforderlich. Allerdings gibt es Unterschiede zwischen den verfügbaren Qualitäten und Typen.
Wir empfehlen daher, vor der Herstellung Ihrer Produkte zu prüfen, welche Art von MDF-Platte Sie verwenden möchten.
Außerdem empfehlen wir einen klimatisierten Lagerraum, um den Feuchtigkeitsgehalt der MDF-Platten zu steuern.
Ist der Ofen, den ich für die Pulverbeschichtung von Metall verwende, auch zum Aushärten von MDF-Platten geeignet?
Die meisten herkömmlichen Aushärteöfen sind Konvektionsöfen. Die besten Ergebnisse für MDF-Platten werden mit Infrarot-Öfen erzielt.
Damit kann die Oberfläche der MDF-Platten schnell zum Aushärten der Pulverbeschichtung erhitzt werden, während der Kern relativ kühl bleibt.
Weil es bei Konvektionsöfen länger dauert, bis die Aushärtungstemperatur erreicht ist, sind die Temperaturen oft zu hoch oder der MDF-Kern erwärmt sich zu stark.