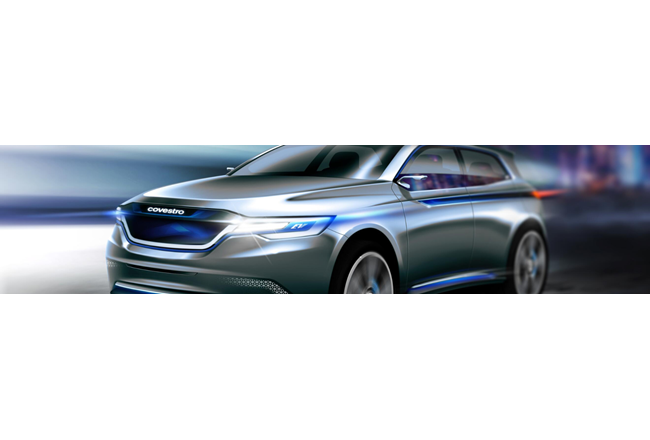
Innovative Forward Automotive Lighting Design with Laser Welding Technology
Our team initiated a project to propel mono-material headlamp technology forward by introducing laser welding as a more sustainable alternative to adhesive bonding. This collaboration with Emerson, a global technology company, promotes cost savings, weight reduction, and sustainability advantages through mono-material design.
Simultaneous laser welding has become a benchmark technology for welding of tail lamps. With the innovative material combination and unique mono-material concept developed by Covestro, it's now possible to extend benefits for laser welding from rear of the vehicle to front lightning applications.
Headlamp assembly typically relies on adhesive bonding, but laser welding presents a more sustainable option. The development of advanced headlamp systems incorporates high-performance materials such as Makrolon® and Bayblend® to enhance overall performance.
By introducing laser welding, the goal is to enhance the efficiency and performance of headlamp manufacturing. This transition not only promotes significant cost savings but also contributes to weight reduction, leading to improved vehicle fuel efficiency. Additionally, the use of laser welding aligns with sustainability goals by reducing the environmental impact associated with adhesive materials.
The Branson laser welding technology in combination with the unique properties of Makrolon® excelled across diverse testing scenarios, demonstrating the feasibility of a mono-material headlamp and innovation in automotive forward lighting.
These collaborative efforts have resulted in groundbreaking advancements in automotive forward lighting design. By leveraging polycarbonate materials, advanced thermal conductivity, and laser welding technologies, these innovations promise enhanced sustainability, cost efficiency, and performance across the automotive industry.
Through this partnership, Covestro and Emerson are setting new benchmarks in automotive lighting, driving the industry towards a more sustainable and efficient future.
We combined creative design, advanced processing techniques and high-performance resins to demonstrate the suitability of a mono-material headlamp, but these concepts can be applied to different vehicle applications as well.
Key Benefits
- Sustainability Enhanced recyclability compared to adhesives
- Precision Precise control over welding area
- Cost effective Reduces material usage and increases production