
Electric Car Components
Featured Brands
- Apec® is Covestro brand for high-performance polycarbonate specialties, addressing complex requirements through advanced technology.
- Versatile toughness via blends of PC+ABS; PC+ASA; ABS+PC and PC+SAN
- Baydur® – the versatile polyurethane that meets the needs of a variety of applications
- Energy-absorbing PU foam for passive safety systems
- Polyisocyanates for a wide range of PU foams, coatings and adhesives
- Prepolymers for low-VOC elastic sealants and adhesives
- Smart combinations of polycarbonate and polyester in ultra-tough materials
- High-performance polycarbonate for applications in diverse industries.
Key Benefits:
- Lightweight: Stiff, light composite materials reduce electric vehicle battery and component weight.
- Safe: Our EV battery packaging is impact-resistant and can be tailored to any cooling system.
- Cost-effective: Durable electric powertrain parts use mass production technology.
- Easy to manufacture: Materials are formable, strong and well-suited to EV components with modular design.
- Reliable: Optimized adhesion to interface materials to ensure the mechanical integrity of the pack
Mobility undergoes a profound change as public and government initiatives seek to replace the combustion engine with sustainable alternatives. Electric vehicles (EVs) require high-performance batteries, crash-safe structures, effective battery cooling, and stable powertrain components. Our materials and coatings empower manufacturers to create enhanced EVs.
Fitting numerous fast-charging cells into an electric car battery necessitates flame-retardant, impact-resistant, and temperature-stable components. Our lightweight Bayblend® FR polycarbonate and ABS blend serve as an ideal solution for cell holders and EV battery modules, maintaining stability at 80°C for optimal efficiency while meeting the UL94 V-0 flame retardancy rating. Additionally, our Makroblend® resin provides the durability required for protective housing, withstanding vibration, impact, and abuse testing conditions.
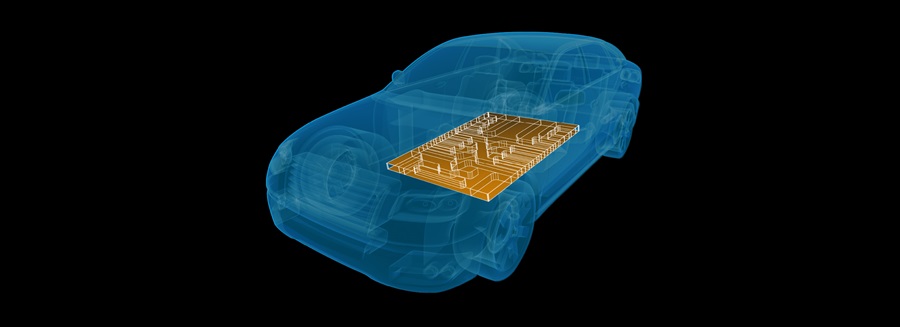
Processing benefits
- Tailored flow properties for filling tight spaces between battery cells
- Short cycle time thanks to adapted foam kinetics
- High automation potential for the foaming process
Product benefits
- Customized formulation to meet individual customer and product requirements
- Lightweight foam solution and efficient material usage
- Encapsulation of cells to protect against mechanical, electrical, and thermal influences
- Strong adhesion to the cell casing and battery housing, promoting the torsional stiffness of the battery pack
- Enables manufacturers to implement a modern cell-to-pack battery architecture
Baypreg® is a Polyurethane spray system and has been designed for lightweight, continuous fiber-reinforced composites. It can be utilized by battery manufacturers to produce battery covers using the Spray Transfer Molding (STM) process, which also allows the integration of a thin steel sheet, if desired.
Processing benefits- Integration of slim flange possible
- Improved production efficiency and low cycle time
- For enhanced mechanical properties, a steel sheet can be integrated during the pressing step
Product benefits
- Lightweight solution
- 1.5 mm part thickness, including the steel sheet
- 60-65 % glass fiber content
- High mechanical strength and stiffness across a wide range of temperatures
- Electrical and thermal insulation

Battery cells require safety measures to prevent risks in terms of thermal runaway caused by a potential mechanical impact from the side or the bottom, e.g., in case of a crash. Covestro has developed Baysafe® EA, a versatile Polyurethane rigid foam, which is tailored to energy absorption. Battery makers may use our molded foam for crash pads to protect their HV batteries in case of exceptional load situations.
Manufacturing advantages- Foaming enables complex and large geometries adapted to the available space
Product advantages
- Lightweight foam solution
- Customized mechanical foam properties
- Lower temperature dependency of mechanical properties compared to most thermoplastics
- Conversion of crash energy into foam cell deformation and heat
- Thermal insulation of battery
As electric car battery technology evolves, lightweight modular, extendable frames andreinforcement beams enable manufacturers to meet future performance demands. Pultrusion stands out as a proven, cost-efficient manufacturing process for creating these composite parts from polyurethane resin and glass or carbon fibers. Baydur® PUL has been designed to support battery manufacturers to meet the increasing battery requirements.
Product advantages
1) Cell safety and protection
- Reduce a potential intrusion of the side wall due to a side impact
- Inner struts can maintain the integrity of the pack side walls
2) Pack geometric integrity
- Reduce a potential deformation of the bottom plate due to the cell weight
- Reinforcement struts are capable to transfer high loads

Electric cars are steering a transition from semi-crystalline to amorphous materials in powertrain components. These components, ranging from high voltage plugs to sensors, converters, inverters, and bus bars, require enhanced dimensional stability, minimal warpage, reduced humidity absorption, and resistance to electronic corrosion. Our Apec® FR, Bayblend® FR, Makroblend® FR, and Makrolon® TC offer an extensive array of materials meeting these specifications, featuring isotropic shrinkage and phosphorous-based flame-retardancy without susceptibility to electro corrosion
High-speed charging poses a risk of overheating electric car batteries, optimal at temperatures under 40°C for peak efficiency and longevity. Our battery packaging aligns with effective thermal management strategies. Bayblend® FR4065 EV maintains strength when in contact with water/glycol battery coolants. Flame-retardant Bayblend® FR3042, FR3080 EV, and FR 3040 are suited for air-cooled systems. Specific grades of Makrolon®, Bayblend®, and Makroblend® exhibit chemical resistance to phase change materials. Makrolon® TC grades provide enhanced thermal conductivity while maintaining flow and ductility.
Covestro presently provides high-performance polyurethane raw materials to meet the current standards for thermally conductive structural adhesives, gap fillers, and sealants used in the assembly of EV battery packs.
- Desmodur® E: Our broad portfolio of aliphatic and aromatic prepolymer solutions boasts a high degree of formulating latitude.
- Desmodur® ultra: Our ultra-low monomer content polyurethane hardeners can be used to improve the industrial hygiene profile of formulated products used in EV battery applications.
- Desmoseal® S: Our Silane Terminated polyurethane technology offers improved adhesion performance on a wide range of substrates coupled with an alternative silane curing technology