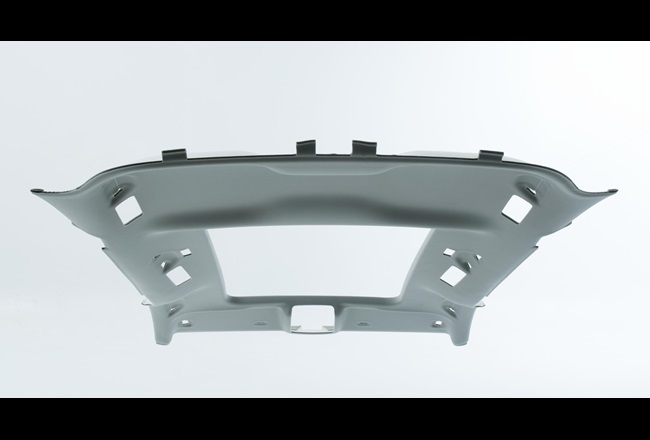
Second life in high-value applications for Baynat® Polyurethane (PU) foam production waste
New ways to re-utilize production waste from Baynat® headliner production
During Polyurethane processing a certain amount of scrap, like cutting and punching waste is often unavoidable. As one example, in processes involving the production of Baynat® core foam for automotive headliners, 10-15% of this high-purity precious material is being wasted. Instead of thermally recovering polyurethane, International PUR, customer of Covestro, has found an innovative and cost-efficient way to re-utilize Baynat® foam production waste, which is used in high-quality applications such as precise prototype and production support tools for its own use or at customers. The technical solution from International PUR is a great example of how innovative business models are born out of a challenge.
Material properties of Baynat® play a vital role in providing great solutions
To bridge the gap to future chemical recycling and to prevent thermal recovery, innovative ways and business models need to be identified to make the most of Baynat®’s reliable thermal and mechanical properties in second-life applications.

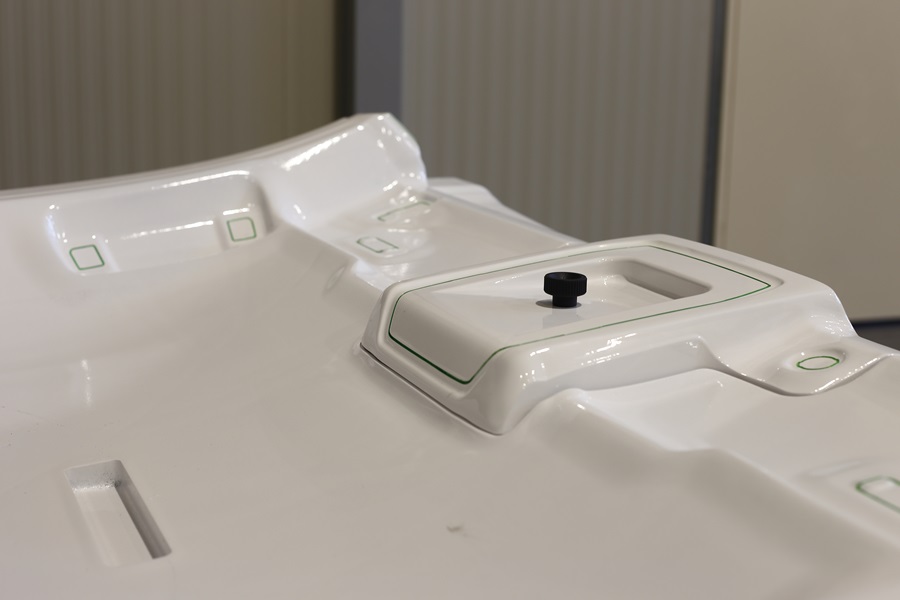
Can PU waste from Baynat® headliner production push boundaries and improve sustainability?
Reusing PU production waste can contribute to meeting the sustainability goals. The extended lifetime of Baynat® waste implies delayed CO2 emissions, thanks to the technology developed by International PUR.
This valuable and cost-efficient material can substitute aluminum and conserve other resources while also reducing waste that arises during CNC processing of tools. PU waste is not thermally recovered immediately, but instead remains longer in the use phase.
Moreover, upgrading PU waste and selling it for value-added, second-life applications presents an additional business opportunity for any customer of Covestro.
Reusing PU waste from Baynat® headliner production for a positive impact on mobility
“Covestro is intensively working on solutions for the chemical recycling of PU production and end-of-life waste. Until these technologies are ready for large-scale recycling, new ways have to be found. The approach of reusing automotive headliner core foam production waste developed by International PUR, is a great example of innovative ways and business models to give high-performance PU production materials a second life in value-added and high-quality applications, while at the same time contributing to a more sustainable business.”
Key Benefits
- Save resources: Potential to substitute aluminum required for support and prototype tools.
- Cut aluminum waste: Potential to eliminate aluminum waste in tool production.
- New business models: Semi-finished recycled PU boards can be sold to third parties for tooling.
- Positive impact: Reusing PU waste is a step ahead in mobility and environmental solutions.