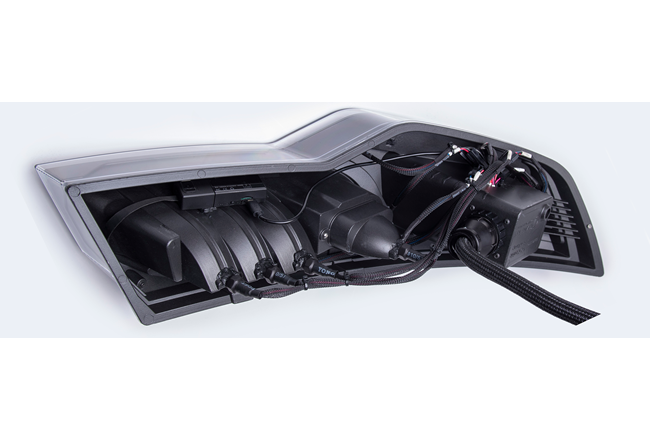
Tailored solutions for future LED headlamp housings and reflectors
An upgraded headlamp housing
Future automotive headlamps will integrate electronic applications such as LiDAR, radar and cameras in addition to LED and other light sources. This will increase localized heat generation and require use of a thermally conductive polymer to manage the heat generated by these electronics. The headlamp demonstrator is the first of its kind to do so with Makrolon® TC polycarbonate.
The low- and high-beam lamp modules, LED strips and sensor element are mounted directly to the surface of the thermally conductive Makrolon® TC polycarbonate housing for improved heat management and reduced system complexity.
The selected housing material enables stable mounting of LiDAR, radar and camera sensors. Makrolon® TC polycarbonate exhibits improved stiffness over a broad temperature range, allowing a dimensionally stable LiDAR housing interface that aids LiDAR accuracy. The material’s flexural modulus minimizes the LiDAR system’s exposure to vibrations, improving LiDAR accuracy and reducing signal noise.
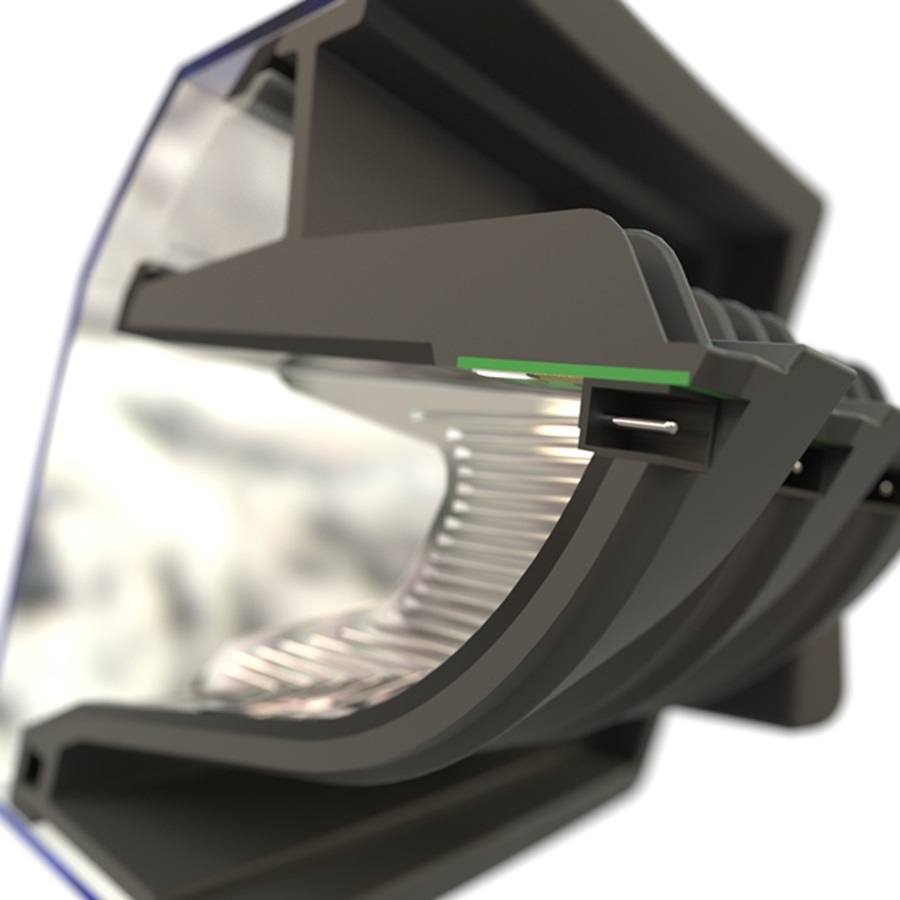
A brighter, lighter headlamp
In-mold electronics (IME) enable the LED electronics to be molded directly onto the Makrolon® TC polycarbonate housing in one step. Eliminating additional processing steps enables a less expensive subassembly through part count reduction and elimination of added heat sinks and fasteners.
The low- and high-beam reflectors utilize Makrolon® DS polycarbonate for highly efficient reflectivity of visible light. The reflectors can be formed directly to the Makrolon® TC polycarbonate housing with multi-shot molding and vario-thermal mold temperature control techniques. This combines thermally conductive and metalizable materials into one part, removes the need to attach the reflector with brackets and fasteners, contributing to lightweighting and reduction of the overall depth of the headlamp assembly by several centimeters.
The Makrolon® DS polycarbonate material provides a metalizable, smooth surface finish to enable greater lumen output. In fact, the single, metalizable component yields a beam pattern performance that remains stable throughout the operating temperature of the LED lamp system due to its low, isotropic thermal expansion.
A perfect material match
The thermal expansion of the housing’s Makrolon® TC polycarbonate and the reflector’s Makrolon® DS polycarbonate match very well. This results in improved photometrics over other material combinations for the housing and reflectors, respectively.
Future automotive lighting applications need innovative materials that can contribute to increased heat management and higher lumen output. Covestro polycarbonates, combined with innovative design and processing techniques, including part reduction and integration, can help OEMs and their suppliers maximize performance while reducing headlamp system complexity, cost, weight and volume.
- Improving production efficiencies Makrolon® polycarbonate and supporting molding techniques allow for component and process consolidation, reducing costs
- Drive lightweighting Lightweight polycarbonate materials provide high part performance while reducing part weight
- Improved performance Achieves a high lumen output and manages heat dissipation
- Lower complexity Part and process consolidation minimizes manufacturing operations