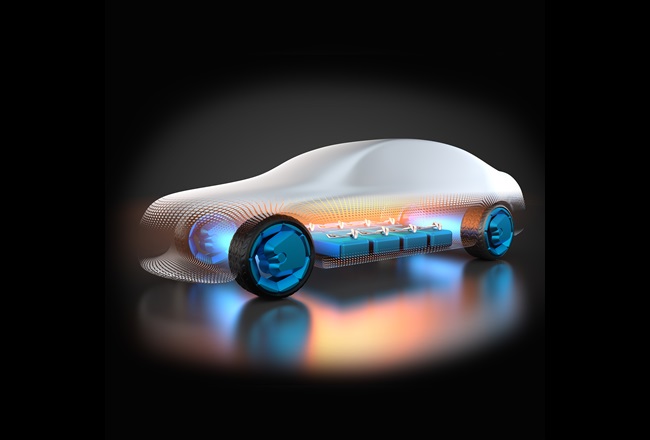
Driving for a safer electric car
Driver and passenger safety is at the heart of our latest innovations in eMobility.
In the face of climate change and increased regulation, the use of electric cars is expected to grow significantly in coming years. Yet while sustainable mobility solutions are crucial, OEMs also need to ensure that safety remains paramount.
Our polyurethane composite materials aim to do just that, by using Baydur® PUL pultrusion technology to develop a new battery pack that is proven to be safer than other packs in key crash tests.
Pultrusion is a well-established and cost efficient manufacturing process, used to create composite parts from polyurethane resin and fibers such as glass or carbon.
Battery housings must be strong enough to protect internal parts from temperature, moisture and extreme loads experienced in a crash.
Benedikt Kilian, Processing Development Expert explains "This new, cost efficient process is ideal for the electric vehicle era as automotive manufacturers require lightweight, strong and modular designs for future purpose-built vehicles."
“Our project showed that advanced composite materials can continue to drive innovation in the automotive industry. We now know that pultrusion can offer increased crash protection to a battery pack, creating a world of opportunities for future electric vehicles.”
Designed for strength
“This new, cost efficient process is ideal for the electric vehicle era as automotive manufacturers require lightweight, strong and modular designs for future purpose built vehicles.”
Key Benefits
- Strong and durable High mechanical strength and structural stiffness leads to a significant improvement in crash protection.
- Proven safety Glass fiber reinforced pultrusion performed better than standard solutions in the simulations.
- Modular The design allows for pultruded panels to be used modularly, allowing for the same part to be used for large and small battery packs.