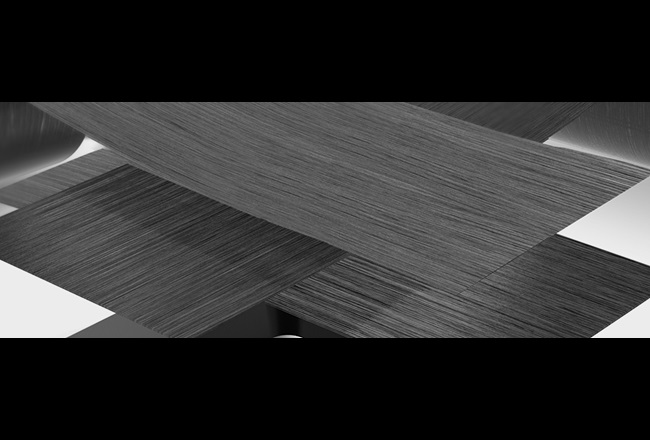
Unlocking the potential of composites to cut costs and increase sustainability
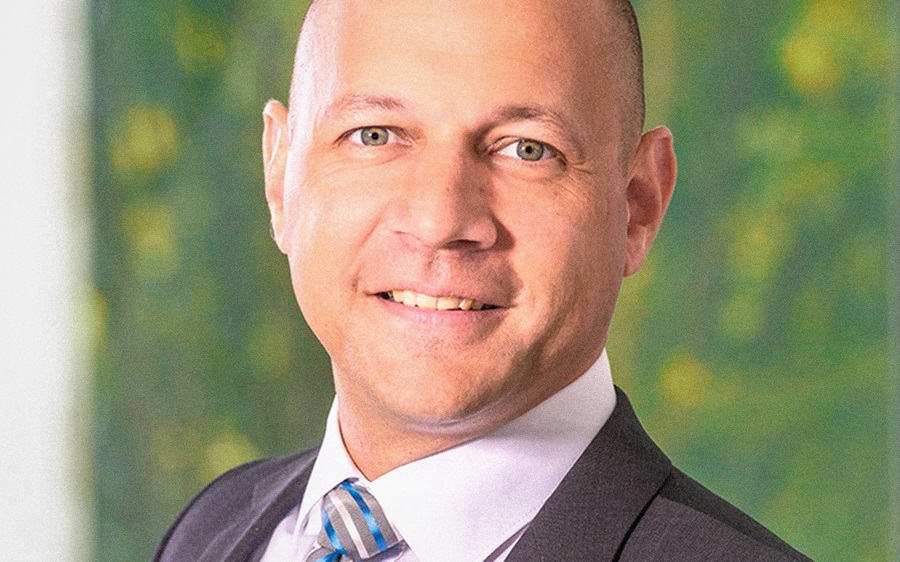
Thermoplastics automatically increase savings because they are easier to process thanks the material properties are not as dependent on processing compared to cross-linking thermosets. And their cost-saving potential is further enhanced with integration of functional elements during injection molding.
Additional material efficiencies can be achieved by manufacturing laminates in near net shape to reduce scraps and ensure load optimization according to a processors’ needs. Material suppliers have the economy of scale to utilize the potential in scrap reduction and load optimization to get costs down by providing tailored laminates.
Different materials offer different benefits, which is why holistic thinking and collaboration along the value chain is so important. It requires a multi-material design approach that supports material optimization by using the right material in the right place to achieve performance improvements, weight savings and cost reductions all at once.
The composites industry is readying itself for increased demand for vehicle lightweighting materials in the high-volume automotive market. However, to ensure a real breakthrough in the mass adoption of composite parts, materials need to be truly cost-competitive when compared to steel and aluminum, according to Dr. Kai Fischer, Scientific Director at the Institute of Plastics Processing (IKV) at RWTH Aachen University and Director of Production Technology at the Aachen Center for Integrative Lightweight Production (AZL). “Instead of asking the automotive industry to pay more for lightweighting, we need to offer composites as a cost reduction material with the additional benefit of light weight,” said Dr. Fischer.
My vision is one day we will have composites all around us in an integrated multi-material system that uses composites because they make parts better and cheaper.
At the end of their working life, thermoplastic composites can be reground and used in an injection molding process for chopped fiber composite materials. Beyond reuse in injection molding, advanced solutions, such as cost-effective fiber extraction, also exist. Either way, the end of one product is potentially the foundation of another.
Like every other industry, technologies in the composites industry are emerging so fast that even big companies are not capable of developing every technology alone: “The biggest potential for innovation lies in the entire value chain working together to come up with disruptive solutions. That’s why we are committed to innovation platforms like IKV and AZL to bring composites to the mainstream through cost reduction and integration with other materials,” said Arne Boettcher, Composites Market Development Manager from Covestro.
Key benefits
- Highly cost-competitive compared to steel and aluminum
- Strong as metal while being extremely lightweight
- Use in lighter vehicle components lowers energy consumption
- Easier to process compared to cross-linking thermosets
- Materials can be easily recycled making them highly sustainable