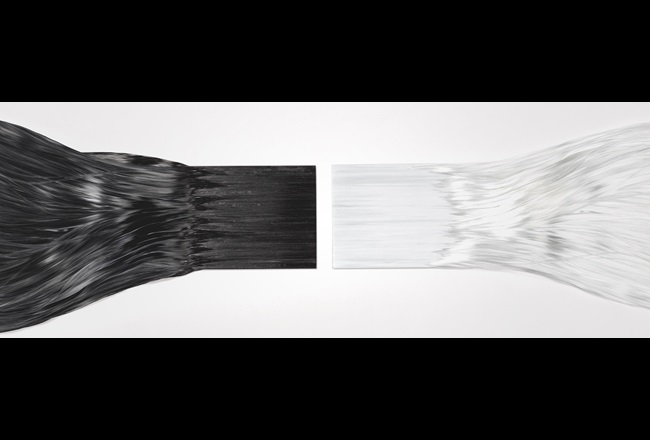
Erschließung des Potenzials von Verbundwerkstoffen, um Kosten zu senken und die Nachhaltigkeit zu verbessern
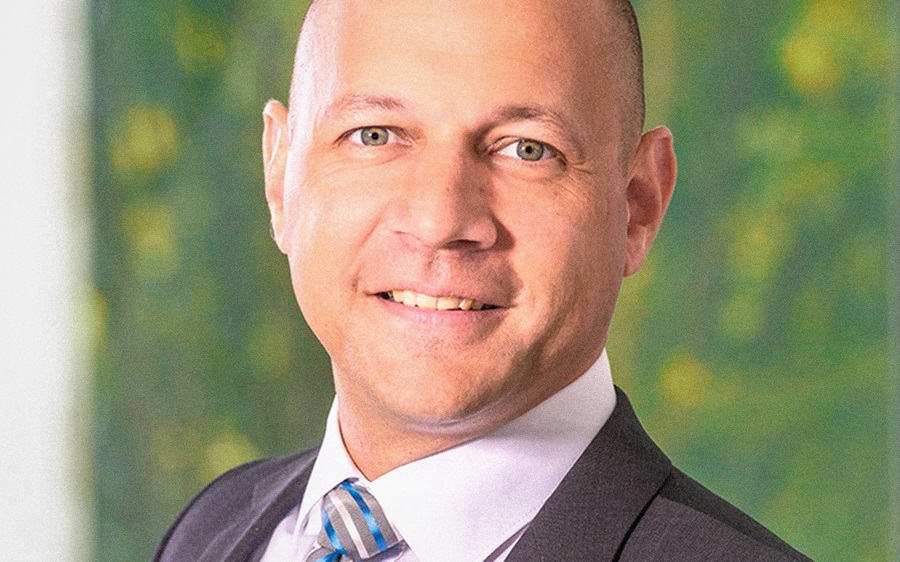
Thermoplaste erhöhen automatisch das Einsparpotenzial, da sie sich aufgrund ihrer Materialeigenschaften im Gegensatz zu vernetzenden Duroplasten leichter verarbeiten lassen. Weitere Kosteneinsparungen können durch die Integration von Funktionselementen während des Spritzgießens erzielt werden.
Verbessert wird die Materialeffizienz auch mit der Herstellung von Laminaten in endkonturnaher Form, um Reste zu reduzieren und die Lastoptimierung entsprechend den Anforderungen des Verarbeiters zu gewährleisten. Werkstofflieferanten können sich Skaleneffekte zunutze machen, um das Potenzial von Abfallreduzierung und Lastoptimierung auszuschöpfen und durch maßgeschneiderte Laminate die Kosten zu senken.
Verschiedene Werkstoffe bieten unterschiedliche Vorteile und aus genau diesem Grund sind eine ganzheitliche Denkweise und Kooperation entlang der Wertschöpfungskette so wichtig. Gefragt ist ein Ansatz für das Multi-Material-Design, der die Werkstoffoptimierung durch Einsatz des richtigen Materials an der richtigen Stelle unterstützt, um gleichzeitig Leistungsverbesserungen, Gewichtseinsparungen und Kostensenkungen zu erreichen.
Die Verbundwerkstoffindustrie bereitet sich auf die steigende Nachfrage nach Werkstoffen für den Fahrzeugleichtbau im volumenstarken Automobilmarkt vor. Laut
Dr. Kai Fischer, wissenschaftlicher Direktor am Institut für Kunststoffverarbeitung (IKV) an der RWTH Aachen und Bereichsleiter Produktionstechnologie am Aachener Zentrum für integrativen Leichtbau (AZL), müssen Werkstoffe jedoch im Vergleich mit Stahl und Aluminium wirklich wettbewerbsfähige Kosten bieten, um einen tatsächlichen Durchbruch bei der Einführung von Verbundteilen im großen Maßstab zu gewährleisten. „Anstatt die Automobilindustrie zu bitten, mehr für Leichtbauwerkstoffe zu zahlen, müssen wir Verbundwerkstoffe als kostensparende Materialien mit dem zusätzlichen Vorteil der Gewichtsreduktion anbieten“, meint Dr. Fischer.
Meine Vision ist, dass wir eines Tages in einem integrierten Multi-Material-System von Verbundwerkstoffen umgeben sind und diese genutzt werden, weil sie Teile besser und günstiger machen.
Am Ende ihrer Lebensdauer können thermoplastische Verbundwerkstoffe gemahlen und in einem Spritzgießverfahren für zerkleinerte Faserverbundwerkstoffe verwendet werden. Neben der Wiederverwendung beim Spritzguss sind auch andere fortschrittliche Lösungen wie die kosteneffektive Faserextraktion möglich. Das Ende eines Produkts ist in jedem Fall der Grundstein für ein anderes.
Wie in jeder anderen Industrie kommen auch in der Verbundwerkstoffindustrie so schnell neue Technologien auf, dass selbst große Unternehmen nicht jede Technologie alleine entwickeln können: „Das größte Innovationspotenzial besteht, wenn die gesamte Wertschöpfungskette gemeinsam an der Erarbeitung bahnbrechender Lösung mitwirkt. Um den Einsatz von Verbundwerkstoffen durch Kostensenkungen und die Integration anderer Materialien zu verbreiten, arbeiten wir mit Innovationsplattformen wie dem IKV und AZL zusammen“, erklärt Arne Boettcher, Composites Market Development Manager bei Covestro.
Wesentliche Vorteile
- Sehr kostengünstig im Vergleich zu Stahl und Aluminium
- Stabil wie Metall und dabei extrem leicht
- Einsatz in Fahrzeug-Leichtbauteilen senkt den Energieverbrauch
- Einfachere Verarbeitung verglichen mit vernetzten Duroplasten
- Materialien können einfach wiederverwertet werden und sind dadurch äußerst nachhaltig