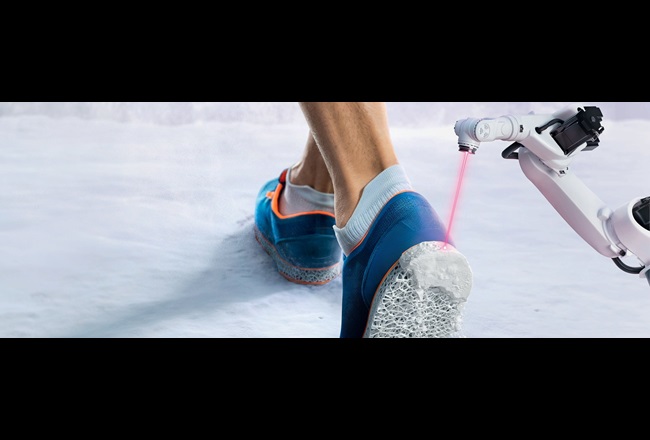
Personalized support for the unique needs of every runner
Industrial 3D printing brings new possibilities to athletic footwear
Athletic footwear is a fast-paced industry with a constant drive to innovate. New shoe designs and materials hit the shelves each year. Innovative production techniques such as TPU-based knitted shoe uppers cut waste in production and eliminate process steps for greater efficiency.
Now, with more and more consumers willing to invest in high-quality individual gear, the industry is looking for ways to achieve the shift from mass production to mass customization.
When choosing a shoe, runners often rely on specialty retailers who offer services such as foot mapping or gait analysis. In the end, however, every single runner is forced to settle in some way. That’s simply because running shoes are made for abstract running profiles and general categories and not for the specific needs of real runners.
But what if athletes could purchase a shoe that was custom-manufactured for their feet on demand and within minutes? It’s a vision that could soon be possible as more and more sports shoe manufacturers adopt solutions from the world of 3D printing.
By printing a certain structure, the shape and hardness can be adjusted in every part of the shoe sole. The result is a shoe that perfectly supports the foot where it’s needed and gives the runner a comfortable and safe running experience.
Depending on the runner’s foot structure and running technique, the midsoles can be designed for highly individual factors such as foot or heel strike, body weight or the demands of specific sports. 3D printed midsoles can be micro-engineered at certain points along the sole to provide either more flexibility or more support. Lukas Breuers, Marketing Manager at Covestro explains, “By printing a certain structure, the shape and hardness can be adjusted in every part of the shoe sole. The result is a shoe that perfectly supports the foot where it’s needed and gives the runner a comfortable and safe running experience.”
This capacity for variation sets 3D printing apart from techniques such as injection or compression molding which do not allow for property variations within the same structure. Additive manufacturing also enables the production of completely new and highly complex geometries. Intricate lattice structures, for example, can be equipped with spatially varying viscoelastic properties for the perfect balance of cushioning and rebound behavior.
3D printed midsoles can be built layer by layer using a wide variety of printable materials. Finding the right material for the process can often pose a challenge, which is where Covestro supports manufacturers looking to leverage the benefits of 3D printing for their applications.
Our versatile polymers and expertise for customized athletic footwear
Covestro offers a versatile toolkit of production-grade polymers for all major additive manufacturing techniques. Thermoplastic polyurethane (TPU), for example, is a well-known solution for footwear applications and highly valued for its inherent mix of flexibility and strength. Our TPU elastomers can be integrated in fused filament fabrication or powder bed fusion processes. We also offer tailor-made polyurethane systems for stereolithography (SLA) and digital light processing (DLP) which rely on light beams to cure photopolymer resins.
Our printable materials can be adapted to support a multitude of properties such as adjustable hardness and cushioning behavior, flexibility over a wider temperature range as well as resistance to chemicals and wear. Many of our solutions support high recycling rates of leftover materials after the 3D printing process, leading to more efficient production.