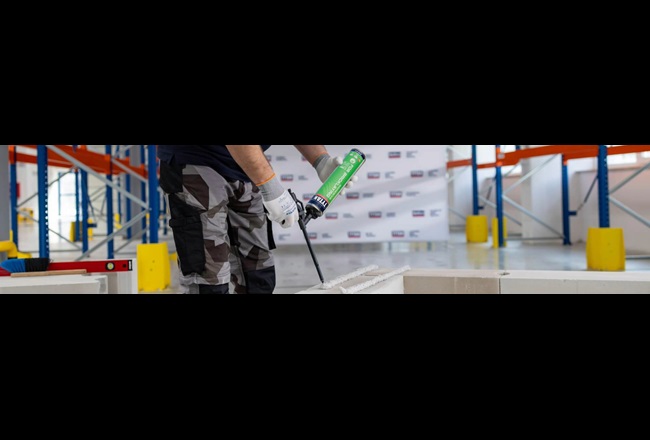
Mass balance MDI enables foam adhesive for bricklaying
The buildings sector accounts for a significant share of greenhouse gas emissions. Reducing its large-scale environmental impact means more than just making buildings energy efficient for their operating life. As operating efficiency rises, attention is turning to the carbon footprint of the actual construction materials.
We are partnering with the Selena Group, a Poland-based leader in construction chemicals in over 100 markets, to spearhead a shift to fundamentally more sustainable construction materials that offer the same performance as fossil-based alternatives.
Our joint vision is to meet European Green Deal energy efficiency goals and drive the wider transition to net-zero carbon emissions for the buildings industry by 2050. In fact, our Desmodur® CQ MB mass balance MDI has already enabled Selena to create its enhanced low-carbon Ultra Fast 70 foam insulation for cavities around windows and doors.
For this project, we focused on creating a more sustainable alternative to replace cement mortar; a raw material that is widely used in the built environment, and one with a high carbon intensity in its manufacturing process.
Materials will play a decisive role in a more climate-neutral and circular economy. If raw material providers in the value chain join forces for climate neutrality, the impact on end products will be significant. That’s why we are very happy to deepen our collaboration with the Selena Group.
The challenge here was to create a viable alternative to conventional concrete mortar with a much lower environmental impact. This new option would have to significantly reduce CO2 emissions, yet fit easily with current building methods, while also offering high adhesion and quick curing times on site.
Using a polyurethane (PU) foam adhesive for bricklaying showed clear potential here, building on our recent experience with Selena on their low-carbon foam insulation. Our Desmodur® CQ MB bio-attributed MDI (methylene diphenyl diisocyanate) offered a low-carbon feedstock for a foam adhesive that could offer easy on-site application at a wide range of temperatures, along with quick curing and a durable bond. This plant-based MDI feedstock could be attributed to the final adhesive product using the ISCC Plus standard, which defines how to track renewable inputs through unified chemical processes. This mass balance MDI offers the same technical performance as fossil-based raw materials.
Climate neutrality regulations in the construction sector mean a steeply rising demand for sustainable building materials. With a great partner like Covestro, we are jointly driving innovation in construction materials with products that put us ahead of the curve with their low carbon footprints.
Selena Group created their high-performance foam adhesive for bricklaying using our Desmodur® CQ MB low-carbon MDI. This bio-attributed MDI emits 60% less CO2 2 than fossil-based MDI. What’s more, in a head-to-head comparison, a single 750 ml can of the final product, Tytan Professional® Adhesive for Bricklaying foam, causes 90% less CO2 emissions than one and a half 25 kg bags of conventional cement mortar. The new product carries ISCC Plus certification, ensuring accurate allocation of the bio-based inputs, and social responsibility3 across the feedstock supply chain.
Beyond emissions reductions, our bio-attributed MDI also gives the final adhesive product other useful advantages: It can be used with high accuracy on a wide variety of brick or construction block materials, from ceramic and silicate to ACC. This level of precision in application also means a higher yield on construction projects than with traditional cement mortars. Importantly, the low-emission adhesive foam also cures twice as fast. Finally, it can be applied on-site in temperatures ranging from -5ºC to +30ºC degrees Celsius, minimizing work losses from extremely low or high temperatures. This low-carbon alternative to concrete mortar is another Covestro contribution to a circular economy and climate neutrality, making the buildings sector more sustainable.
Key benefits
- Low carbon: Our bio-allocated feedstock emits 60% less CO₂ than fossil-based MDI.
- Fast: PU spray foam adhesive cures twice as fast on site as traditional cement mortar.
- Seamless: Mass balance MDI requires no change to formulations or production processes.
- High yield: Precise application to ceramic, silicate or ACC means higher yield than cement.
- High productivity: Can be applied in low and high temperatures from -5ºC to +30ºC degrees Celsius
2 According to an internal calculation by Covestro based on the TÜV reviewed EcoPAss LCA method (ID No. 0000083440).
3 ISCC – International Sustainability and Carbon Certification (ISCC) is a certification system that ensures compliance with high ecological and social sustainability requirements, and traceability throughout the supply chain.