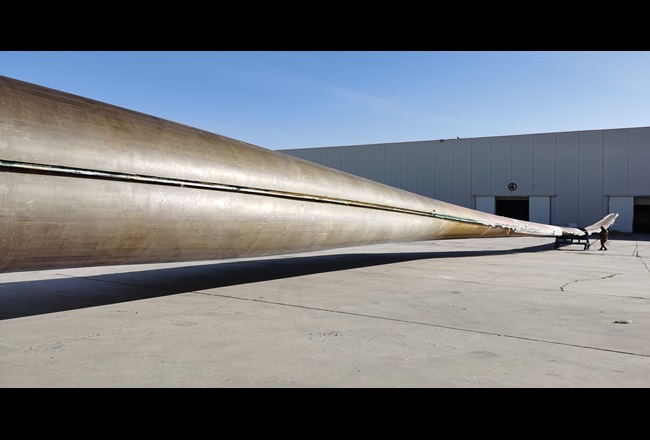
The world’s first 64.2m full polyurethane resin wind turbine blade
As well as having a significant cost advantage over traditional epoxy solutions, tests showed that polyurethane infusion resin also enhances mechanical properties, as well as shortening s curing time and reducing infusion speed. This can improve the efficiency of blade production – thus increasing the competitiveness for blade manufacturers. As such, the production of this blade represents a major milestone in the sustained development of wind power.
“Polyurethane is a very cost-effective material, and can thus provide great support for wind power enterprises when wind power prices reach parity with fossil l power systems after 2020.”
Using this efficient and cost-effective solution for the full PU resin blade paves the way for a new generation of longer and stronger blades for wind turbine manufacturers and wind farmers. It also reinforces our commitment to providing innovative products and cost-effective solutions for the clean energy industry. Birong Wen, head of Goldwind’s wind blade development team, said: “Polyurethane is a very cost-effective material, and can thus provide great support for wind power enterprises when wind power prices reach parity with fossilpower systems after 2020.”
Jitendra Bijlani, Head of R&D at LZ Blades, said: “The improvement of blade production efficiency by using polyurethane not only enhances the blade cost competitiveness, but also becomes the key to serving our esteemed customers with material technology flexibility. This keeps us one step ahead in an increasingly challenging market environment. ”
“We believe Covestro’s solution can greatly contribute to the sustained development of the wind power industry.”
The 64.2-meter blade – from spar cap to the shear web and the shell – was constructed entirely of polyurethane infusion resin, making it the first of its kind for the wind power industry. Extensive static and dynamic fatigue tests have been carried out to evaluate the durability of the wind turbine blade. Small-scale production will be scheduled soon.
“We believe Covestro’s solution can greatly contribute to the sustained development of the wind power industry,” said Dr. Irene Li, Head of Application Development Asia Pacific, Polyurethanes Segment at Covestro.
“The improvement of blade production efficiency by using polyurethane not only enhances the blade cost competitiveness, but also becomes the key to serve our esteemed customers with material technology flexibility. This keeps us one step ahead in an increasingly challenging market environment. ”
Key benefits of polyurethane resin for use in wind turbine blades
- Long blades Covestro polyurethane resin enables the production of long blades. This case demonstrates the ability to produce 64.2m blades only with polyurethane resin, from spar cap to shear web and shell.
- Cost efficient production Compared to traditional epoxy resin, polyurethane infusion resin has very attractive mechanical properties, with a shorter curing time and a faster infusion speed.