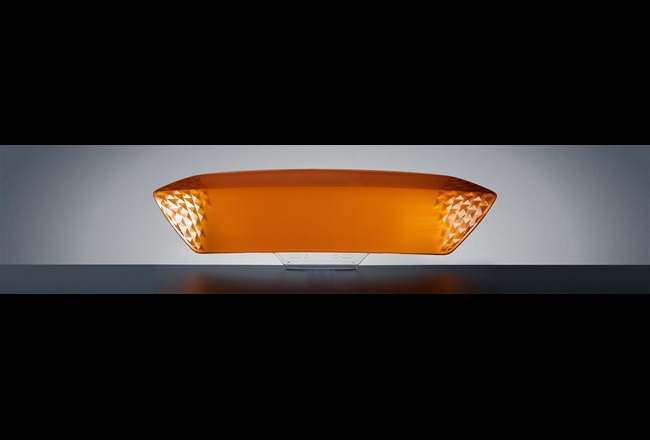
Revolutionizing surfaces: Direct Coating / In-Mold Coating technology
What is Direct Coating / In-Mold Coating
Direct Coating is a modified 2-shot molding process combining injection molding with reaction injection molding in a single mold. This innovative technique involves two key steps:
- Injection of polycarbonate or its blends into the mold
- Overmolding the thermoplastic part with a reactive polyurethane coating system (based on polyol and isocyanate) into a second cavity
Within moments, the polyurethane cures to form a finished, coated part with a flawless surface, free from the dreaded "orange peel" effect.
Unlocking benefits of Direct Coating / In-Mold Coating
Direct Coating isn't just a process; it's a game-changer for the injection molding industry. Here's how it's revolutionizing the manufacturing process:
- Streamlined Production: Direct Coating significantly simplifies the production process by eliminating the need for a painting line.
- Flexibility in Manufacturing: The process enables small lot production of various colors, allowing for greater adaptability to market demands.
- Function Integration and Enhanced Design Freedom: Direct Coating opens new possibilities for product differentiation, enabling a wide range of textures, finishes, and colors. Furthermore, delicate electronics like heaters or LEDs can be overmolded.
- Excellent Surface Quality: Achieve surfaces with superior characteristics.
- Increased Efficiency: The automated process eliminates overspray, works without solvents, removes the need for additional drying processes and simplifies production logistics.
- Reduced Scrap Rates: Experience significantly reduced scrap rates due to an integrated process, contributing to a more sustainable manufacturing process.
- Inventory Optimization: Direct Coating allows for a reduction in working inventories, streamlining the supply chain.
Your partner for Direct Coating / In-Mold Coating
We are providing the technology and so much more! We offer comprehensive support throughout the entire process chain. Our commitment to your success includes the following:
- Expert assistance in part design
- Mechanical and rheological simulations of the thermoplastic and polyurethane component
- Global expertise in molding trials
- Rigorous component testing
- Dedicated support for mass production launches
- Expertise in coating raw materials and polycarbonate
Covestro has filed multiple patent applications and holds several patents related to Direct Coating technology.
With state-of-the-art development centers in Pittsburgh, Shanghai, Leverkusen, and Amagasaki (Japan), our global network ensures the availability of materials and expert guidance for practical trials.
Revolutionizing the process of coating plastic parts
From today’s perspective, we optimized our polycarbonate and PC-blend products for improved adhesion in the Direct Coating process. Furthermore, we're recognizing an exciting trend using Direct Coating in automotive production, signaling a shift toward more efficient manufacturing processes in the automotive industry. Our established Direct Coating process has been successfully used in series production, including for the BMW kidney of the BMW iX with its transparent PUR coating and for the BMW i5 & i7 BMW Interaction Bar interior smart bars with clear PUR coating.
Due to an increasing interest in colored exterior applications, Direct Coating is redefining traditional surface finishing methods. It can be used to apply colored polyurethane to the thermoplastic.
Direct Coating with Mass-Balanced Products at Covestro
Direct Coating can also be used with mass-balanced products from Covestro. Mass-balance focuses on using both renewable feedstocks and energy so that the final product can be certified as having up to 89% sustainable raw materials and a reduced carbon footprint. This decreases the reliance on fossil-based raw materials and reduces the carbon footprint, aligning with customers’ sustainability goals.
At Covestro, we're not just keeping pace with change – we're driving it. Join us in shaping the future of manufacturing with Direct Coating technology.
Key benefits
- Maximum efficiency Automated process with no overspray or solvents
- Streamlined process Short cycle time and no additional drying time needed
- High design freedom Enables high-quality surfaces with custom textures, finishes and transparencies
- Reduced waste Reduction of scrap rates, produced parts require no rework and little finishing