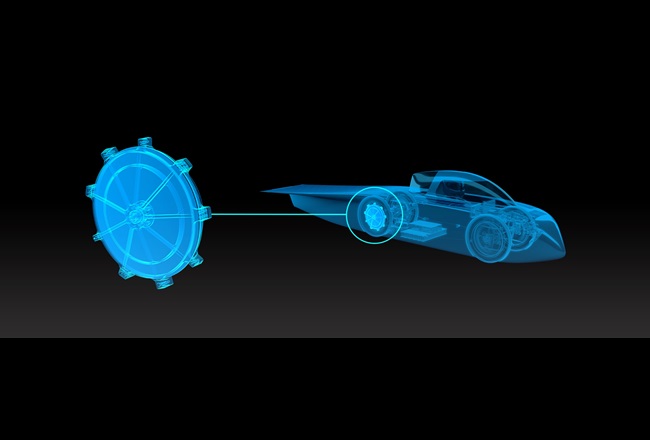
Case study
Desmodur®-based crosslinking technology beats the heat in solar car’s engine
The Sonnenwagen’s original engine was hindered by the maximum operating temperature of the electrical insulating coating used to cast the electrical wires. This year, the team developed a new and improved engine with a copper coil that is fixed and protected by our Desmodur®-based crosslinking technology.
For maximum efficiency, especially at the steep slope of the road, Team Sonnenwagen needed to improve the design of the car’s electric motor to withstand higher temperatures. The team needed a coating technology that could create a heat-resistant, rigid casting that would protect the engine’s copper coils.
Higher heat resistance means that we can put more power into the motor and, as a result, accelerate faster.
The resin that keeps the copper windings of the engine together must resist high temperatures. Polyurethane chemistry has limited temperature stability, so we set out to modify our coating system.
Customers are excited about the high temperature stability of the new material, especially within the field of electrical insulation.
We recently developed a coating system that offers outstanding thermal and chemical stability. We deployed this as a casting resin for the coils in the car’s motor. Based on Desmodur® products, our new crosslinking technology significantly increases the coating’s temperature stability. When compared to traditional 2K polyurethane coatings, this technology goes the extra mile in terms of temperature and chemical resistance as well as mechanical stability.
9qLfA8fX4cjbmtGrcUFJHX
https://asset-out-cdn.video-cdn.net/private/videos/9qLfA8fX4cjbmtGrcUFJHX/thumbnails/567146?quality=thumbnail&__token__=exp=1756634483~acl=/private/videos/9qLfA8fX4cjbmtGrcUFJHX/thumbnails/567146*~hmac=ee00628ad39de54b8a780c5df0b13faaf04330cb125f8f449145eec194e6c9f5
Sonnenwagen_Engine_4th_Episode_LongForm
Why crosslinking technology was the right solution for the engine
- High temperature stability: Features increased temperature stability up to 220 degrees Celsius.
- Chemical resistance: Provides increased chemical resistance, especially against brake fluids and oil.
- Mechanical stability: Offers improved mechanical stability when compared to the previously used cast system.