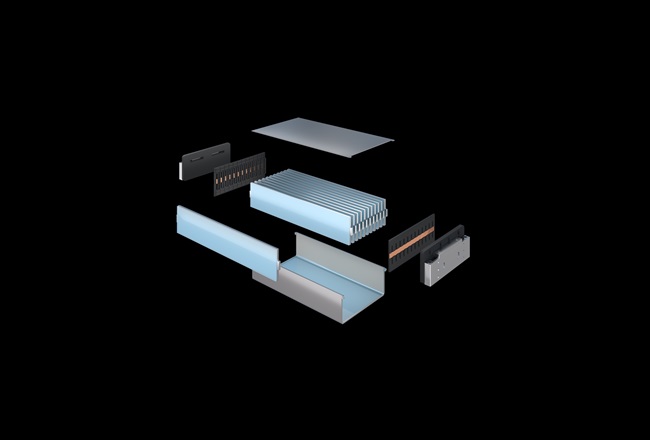
Choosing the right engineering plastics for pouch battery packs
Suitable for laser welding
Laser welding has become the preferred technology to bond tabs and modularize pouch cells. In this application, the ideal solution for tab holders is an engineering plastic that is tough over a wide temperature range (-30 °C to 60 °C). Such material must resist laser welding temperatures over 120 °C. It should be flame retardant and electrically insulating to enhance safety performance. In addition, components must meet tight tolerance requirements, provide predictable cell location and enable repeatable mass production with short cycles times. Demands that can only be met by a tough and high-heat engineering plastic with outstanding dimensionally stability.
Battery electrodes protection
To design high quality pouch modules, the battery electrodes must be carefully protected. Designers must balance creepage distance and space utilization, energy density and durability. Thin sections, precise sub-millimeter locating features and snap fits are also common. Both electrical and mechanical properties play critical roles in selecting the most suitable materials.
Pouch cells are core elements of the battery and key to EV performance. In close collaboration with battery designers, Covestro’s Battery Packaging Team helps pouch cells deliver their value with advanced packaging components and solutions based on Makrolon® PC and Bayblend® PC+ABS.
Lightweight, electrically insulating hybrid end plates
Components that combine plastics and metals may provide multiple design benefits. They are lightweight, electrically insulating, help reduce part count and increase reliability. Overall, metal-plastic hybrid parts combine the best features of each material in a single component. Compact battery design is sparking an interest for hybrid structural components such as end plates for modules composed of pouch cells. These plates constrain the expansion that occurs during charging and discharging cycles. Plastics used for these applications must have low shrinkage, low coefficient of linear thermal expansion (CLTE) and low internal stress induced at the interlayer with the metal. They must also be flame retardant and electrically insulating.
Key Benefits
- High heat resistance, high impact resistance, high flame retardancy: the tab holders made of Makrolon® FR6005 are suitable for laser welding.
- Excellent electrical and mechanical properties: the electrode protectors made of Bayblend® FR3050 improve design flexibility and safety.
- High strength, high flame retardancy, high flow and low CLTE: the hybrid end plates made of Bayblend® FR3060 EV enable lightweight, compact design.