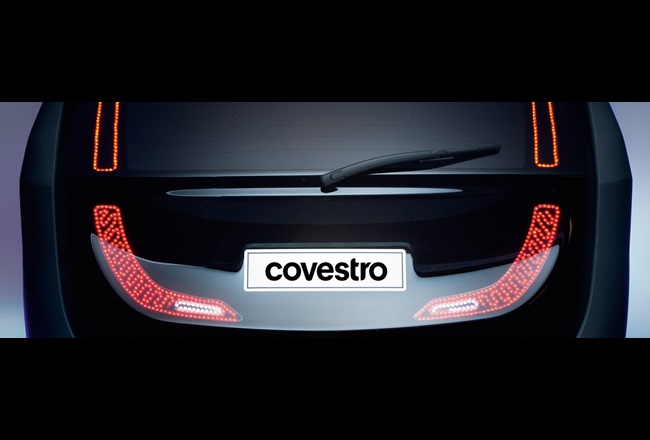
Case study
Makrolon® enables lighter automotive components
As automakers seek ways to squeeze out extra weight from vehicles while maintaining stylish designs, lightweight polycarbonate materials deliver on both counts. Makrolon® is opening up completely new options for the styling and functional integration of automotive components.
Traditional tailgate modules are designed and manufactured with a metal carrier and glass window insert, which can add weight to the vehicle. We tasked ourselves with creating a complete, one-part tailgate with rear light modules and a display made entirely of our lightweight polycarbonate materials.
Because the tailgate would be manufactured as a one-part component, we needed to select a versatile polycarbonate that could be manufactured in a transparent grade. The material would also need to be extremely robust, given the automotive context, and suitable for injection compression molding.
We selected transparent Makrolon® AG to enable a seamless outer skin. Non-transparent areas were back-printed in a dark color or back-injected with a black frame material using two-component injection molding. The rear backlights are part of the polycarbonate skin, making assembly and logistics easier – and more economical – by eliminating the need for separate backlight and display housings. This highly integrated and distinctive tailgate offers clear weight savings over traditional tailgate designs. In the near future, Makrolon® will also help to integrate LiDAR and RADAR sensors as well as cameras into automotive exteriors.
Why Makrolon® was the right solution for our tailgate concept
- Lightweight: Makrolon® offers high performance without weighing down applications.
- Tough: High impact strength satisfies the requirements of automotive parts.
- Customizable transparency: Custom and transparent grades mimic glass and other materials.
- Highly flowable: Suitable for efficient, one-piece injection compression molding.
- Stylish design: Glass-like surfaces in combination with hard coatings.