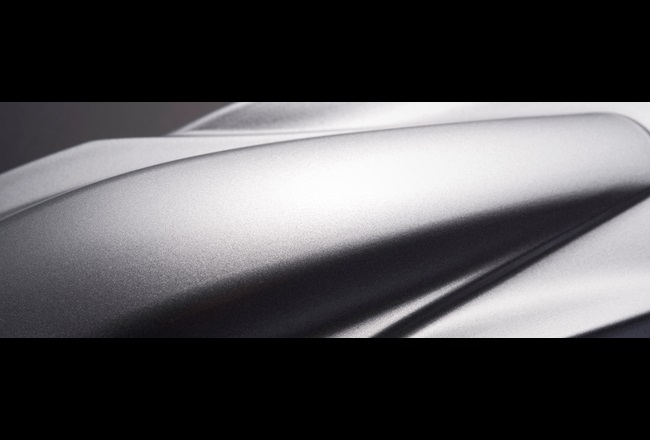
Plastic part design: From concept to commercialization
Product designers and engineers must consider many factors when designing parts made of polycarbonate. These include functional requirements, ergonomics, aesthetics and economics, as well as design stages such as evaluating process options, conducting prototype testing, digital engineering, simulations, and reducing manufacturing costs. A vital part of this process is the evaluation of your part and material requirements, since they impact both part design and the selection of materials.
We also consider factors such as mechanical loading, processing technologies, color needs and surface finish to determine the most appropriate grade of polycarbonate for a particular application. Our wide variety of polycarbonate and polycarbonate blend resins are suitable for a wide range of parts. In addition, we assist customers in material selection, design and production support. This technical support includes CAE, which simulates, validates and optimizes product design and processing.
And there’s still more to part design than the name implies because design isn’t the end; it’s just the beginning. Design should be viewed as an ongoing process that starts with concept development and continues all the way through to fabrication. More specifically, it encompasses initial design, materials selection, planning of manufacture, planning long and short-term structural needs for final assembly, and anticipating potential mold-related considerations such as runners, gating and warpage. The fact that we keep a watchful eye on all these aspects means that you can design parts more successfully and efficiently, and enjoy greater peace of mind too.