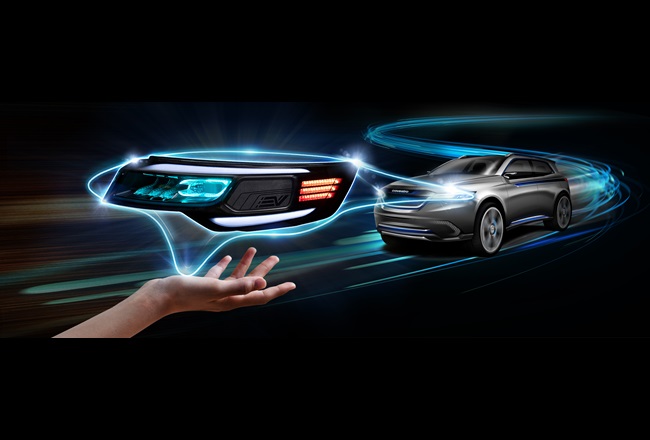
Story
Reimagining automotive forward lighting with polycarbonates
When it comes to materials and technologies for future auto lighting, Covestro is driving ahead of the curve, developing a functional headlamp concept to illustrate how polycarbonates enable functional and aesthetic benefits. This visionary approach can also reduce weight, space and cost while offering greater sustainability.
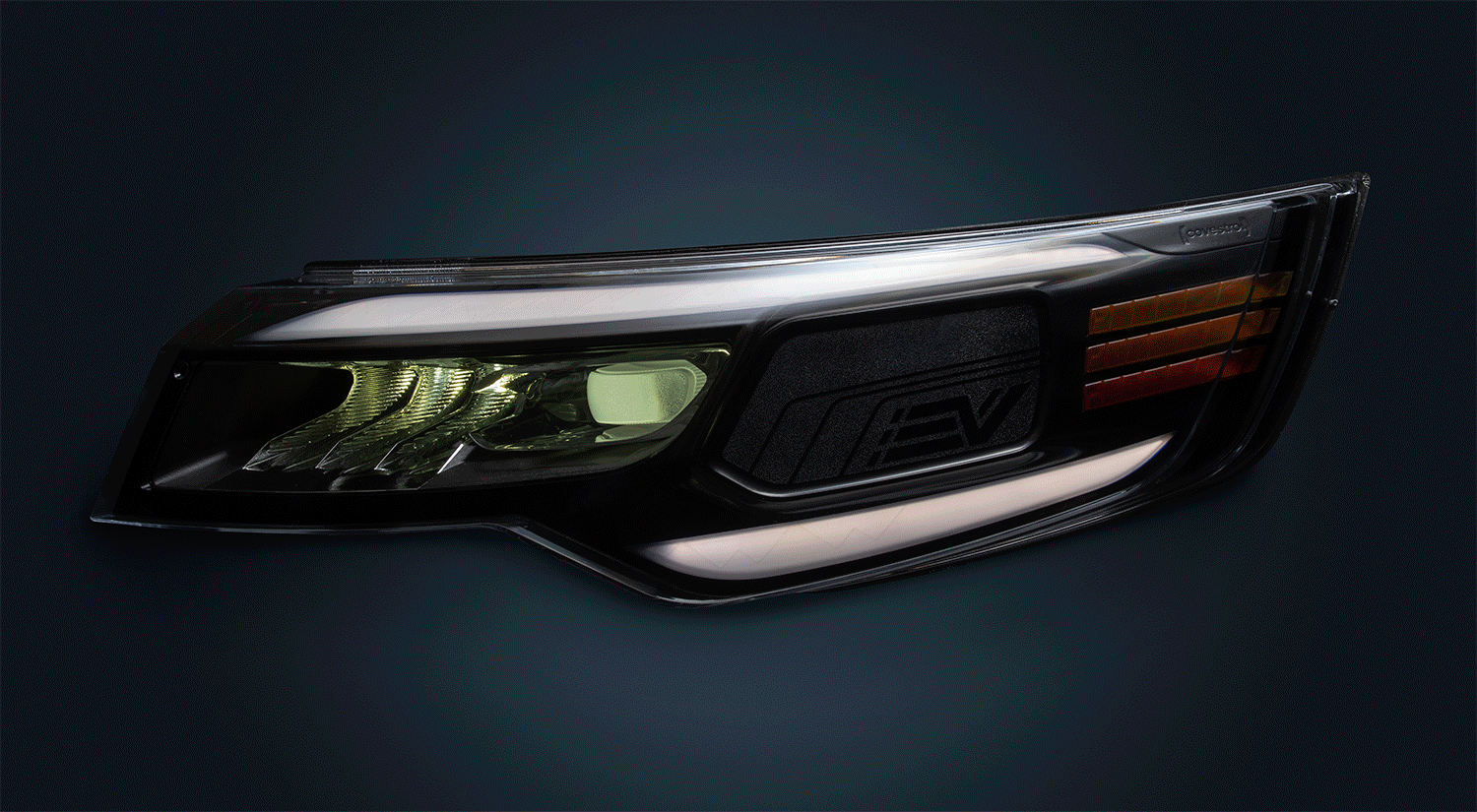
Part consolidation: less is more
Traditional headlamps are complex, usually incorporating dozens of components and screws. Covestro advocates a forward-looking approach to forward lighting, with a headlamp module concept comprised of a reflector/housing, collimator lens, bezel and outer lens cover that results in significantly fewer parts.
Multi-shot molding of Makrolon® TC thermally conductive polycarbonate and Makrolon® DS dimensionally stable polycarbonate, along with a molded-in-place design strategy, enables the low- and high-beam LED modules and their corresponding reflectors to be produced less expensively through elimination of added heat sinks, attachments and other components. The bezel of Makrolon® polycarbonate uses multi-shot molding to consolidate turn signal and daylight running lamps while hiding sensors behind a LiDAR-transparent mask. Beyond reducing system complexity and costs, simplifying assembly and saving valuable space, this novel approach also reduces headlamp weight, which aids better fuel mileage and lower emissions or increased battery range.
9j7xUAs8XFLymByoMSEaoW
https://asset-out-cdn.video-cdn.net/private/videos/9j7xUAs8XFLymByoMSEaoW/thumbnails/1009256?quality=thumbnail&__token__=exp=1754985070~acl=/private/videos/9j7xUAs8XFLymByoMSEaoW/thumbnails/1009256*~hmac=1fc8570529a62af2ad3a3bd01966a3f0f4209031f6d571383320eec4d3c5b5fa
PCS Automotive ISAL video.mp4
Integrating electronics
Future automotive headlamps will integrate electronics such as LiDAR, radar and cameras in addition to light sources. This will require use of thermally conductive materials to dissipate the heat generated by the electronics and light sources. The headlamp demonstrator is the first of its kind to do so with Makrolon® TC polycarbonate.
The low- and high-beam reflectors utilize Makrolon® DS polycarbonate for highly efficient reflectivity of visible light. The reflectors can be molded directly into the Makrolon® TC polycarbonate housing with multi-shot molding and vario-thermal mold control techniques. This eliminates the need to attach the reflector with brackets and fasteners, contributing to lightweighting.
The Makrolon® DS polycarbonate material provides a metalizable, smooth surface finish similar to unfilled polycarbonate and can enable greater lumen output compared to other systems. In fact, the single, metalizable component yields a beam pattern performance that remains stable throughout the operating temperature of the LED lamp system due to its low, isotropic thermal expansion.
The bezel is a three-shot molded part with Makrolon® LED in both amber color for the turn signals and a diffusion color for the DRLs, coupled with Makrolon® using sensor transparent (ST) polycarbonate for the bezel. The bezel hides advanced driver-assistance systems (ADAS) sensors and consolidates daytime running lights (DRLs), turn-signals and pedestrian communication lighting into one part. The bezel blends cutting-edge performance and aesthetics, including a “dead front,” seamless appearance, a high gloss finish enhanced with laser-etched effects, and diffused back-lighting for safety and signature lighting.
Mono-material strategy: good for automakers … and the planet
Due to its smart design, the LED headlamp system uses only four different materials: Makrolon® polycarbonate; Bayblend® polycarbonate/ABS blend, a scratch-resistant coating (outer lens cover) and metallization (reflectors). This simplifies recycling by reducing separation, sorting and storage in the recycling streams at the end of the headlamp’s useful life. The mono-material headlamp is 2-3 centimeters thinner than traditional designs—a designer’s dream! It is also over 1.5 kg lighter, which can help reduce fuel consumption and, therefore, emissions.
This novel headlamp design underscores Covestro’s commitment to sustainability and the circular economy.
Technical support where and when it’s needed
Leveraging its global resources, Covestro collaborates with automakers and their suppliers to implement advanced technologies integrating LEDs, electronics, sensors and other technologies. This includes part and mold design for achieving an optimal balance of performance, aesthetics and economics. The field support Covestro offers helps customers optimize manufacturing processes to maximize productivity and quality.
BQTDUPUyramn_121ELBewx
https://asset-out-cdn.video-cdn.net/private/videos/BQTDUPUyramn_121ELBewx/thumbnails/816609?quality=thumbnail&__token__=exp=1754985070~acl=/private/videos/BQTDUPUyramn_121ELBewx/thumbnails/816609*~hmac=41dcbc305dac7e5e765dd39abda1efa2f84c0cf81b7d355568c9372961eb6d94
PC-centric Headlamp Part 2.wmv
You might say this headlamp prototype is a lighting engineer’s toolbox of unique enabling technologies, allowing OEMs to reduce parts, weight, space and assembly steps–while simultaneously enhancing sustainability. It’s the latest example of how Covestro consistently brings value to our customers.
Key Benefits
- Improve production efficiencies Makrolon® polycarbonate and smart headlamp design reduces parts, streamlines assembly
- Lighter by design Lightweight polycarbonates provide high performance while reducing module weight
- Integrated functions Integrates electronics, such as LiDAR, radar and cameras, as well as light sources
- Greater design freedom Broadens possibilities for aesthetics, progressive styling and differentiation
- Eye on sustainability Reducing weight, parts and materials contribute to greater sustainability