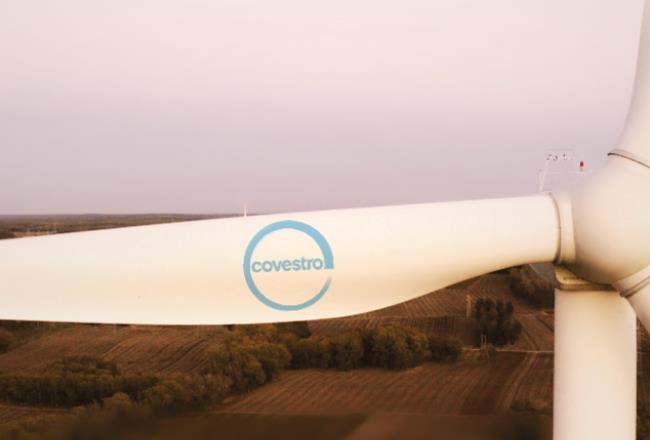
Story
World first PU wind turbine blades: Bigger, better blades with polyurethane infusion resin
The transition to renewable energy sources requires imaginative solutions to meet and, ultimately, become more competitive with non-renewable energy sources. Which is why we are helping to make longer, stronger wind turbines blades with special wind blade resin, such as the 55.2-meter-long blades recently installed in China.
Innovation in wind blades
Inspired by the need for more economical wind energy, we developed a polyurethane infusion resin solution for taller, longer wind blade designs that enhance efficiency and cope with the mechanical stress taller turbines face. Now our resin is proving itself in the field. Turbine blades made with the material have been successfully installed at a wind farm in Tieling, Liaoning Province, Northeast China, which is operated by Liaoning Datang International New Energy Co., Ltd.
The development process involved the participation our R&D teams around the world, which was enabled by close collaboration with partners all along the value chain – and included blade manufacturers, turbine manufacturers, glass fiber producers, machine suppliers and blade designers.
Julien Guiu, Vice President Industrial Marketing APAC, Polyurethanes Business Unit at Covestro, said: “The successful installation of the pilot turbine in Northeast China is recognition of the strengths of our polyurethane infusion resin and demonstrates that it is ready for use in operational wind blades. We hope that this gives a strong signal to our industry partners to manufacture and install longer, stronger wind blades.”
Inspired by the need for more economical wind energy, we developed a polyurethane infusion resin solution for taller, longer wind blade designs that enhance efficiency and cope with the mechanical stress taller turbines face. Now our resin is proving itself in the field. Turbine blades made with the material have been successfully installed at a wind farm in Tieling, Liaoning Province, Northeast China, which is operated by Liaoning Datang International New Energy Co., Ltd.
The development process involved the participation our R&D teams around the world, which was enabled by close collaboration with partners all along the value chain – and included blade manufacturers, turbine manufacturers, glass fiber producers, machine suppliers and blade designers.
Julien Guiu, Vice President Industrial Marketing APAC, Polyurethanes Business Unit at Covestro, said: “The successful installation of the pilot turbine in Northeast China is recognition of the strengths of our polyurethane infusion resin and demonstrates that it is ready for use in operational wind blades. We hope that this gives a strong signal to our industry partners to manufacture and install longer, stronger wind blades.”
Tested and proven
To meet the demand for wind blades that can operate for long periods in harsh conditions, we thoroughly tested the performance of the wind blade materials used in the turbines, and they successfully passed the static test and fatigue tests (both edgewise and flapwise) conducted by China General Certification.
To meet the demand for wind blades that can operate for long periods in harsh conditions, we thoroughly tested the performance of the wind blade materials used in the turbines, and they successfully passed the static test and fatigue tests (both edgewise and flapwise) conducted by China General Certification.
4ns7jgHE7bCSgm5r9QttJv
https://asset-out-cdn.video-cdn.net/private/videos/4ns7jgHE7bCSgm5r9QttJv/thumbnails/422824?quality=thumbnail&__token__=exp=1757090049~acl=/private/videos/4ns7jgHE7bCSgm5r9QttJv/thumbnails/422824*~hmac=edd65b4d8673e40e13759454828ee2fa43a73c2d3cd53aa3d0cadfa2c53e928f
Covestro Wind Blades made of Polyurethane resin are a game changer for the industry EN
How we did it
Wind turbine rotor blades are typically made of fiberglass reinforced resin through vacuum infusion technology. The successful use of polyurethane composite for the production of wind blades suggests that polyurethane resin features superior mechanical properties and anti-fatigue performance. This creative solution for the wind industry also improves production processes in the wind blade factory through a faster curing process and better processing properties that deliver higher levels of productivity.
Wind turbine rotor blades are typically made of fiberglass reinforced resin through vacuum infusion technology. The successful use of polyurethane composite for the production of wind blades suggests that polyurethane resin features superior mechanical properties and anti-fatigue performance. This creative solution for the wind industry also improves production processes in the wind blade factory through a faster curing process and better processing properties that deliver higher levels of productivity.
Moving forward together
In addition to installing wind blades in Northeast China, we entered a cooperation with one of China’s leading wind turbine manufacturers in the development, installation, running and generating of electricity in another 2.2MW turbine with even longer 59.5-meter blades. Over and above this, the turbine’s spar cap, shear web and blade root were all fabricated with our polyurethane infusion resin and the turbine has now been installed in South Central China.
Julien Guiu notes, “With two wind turbines installed in China, we are able to test the operational feasibility and stability of the wind blades in different wind conditions. This will provide valuable data that can inform new blade designs and take us to the next stage in contributing to the advancement of renewable wind energy.”
In addition to installing wind blades in Northeast China, we entered a cooperation with one of China’s leading wind turbine manufacturers in the development, installation, running and generating of electricity in another 2.2MW turbine with even longer 59.5-meter blades. Over and above this, the turbine’s spar cap, shear web and blade root were all fabricated with our polyurethane infusion resin and the turbine has now been installed in South Central China.
Julien Guiu notes, “With two wind turbines installed in China, we are able to test the operational feasibility and stability of the wind blades in different wind conditions. This will provide valuable data that can inform new blade designs and take us to the next stage in contributing to the advancement of renewable wind energy.”
Highlights
PU resin guarantees excellent mechanical performance and other technical benefits that make the production process safer and faster as well as reduce that cost of wind blades. And with blades accounting for around 20-30% of the cost of a wind turbine and around 10-15% of the total wind farm cost, the quicker PU wind blades roll off the production line, the better for manufacturers and wind farm investors.
PU resin guarantees excellent mechanical performance and other technical benefits that make the production process safer and faster as well as reduce that cost of wind blades. And with blades accounting for around 20-30% of the cost of a wind turbine and around 10-15% of the total wind farm cost, the quicker PU wind blades roll off the production line, the better for manufacturers and wind farm investors.
Wind power is unquestionably a critical component of future global energy solutions, but it still has a way to go in terms of matching the efficiency levels of conventional energy sources. The challenge facing us is to find ways to make wind turbines a lot more cost-competitive relative to non-renewable energy sources. More competitive wind blade production will allow an even more significant role in reducing emissions and providing sustainable power to businesses and communities.
The wind industry is pushing the technical boundaries of the blade designers, blade manufacturers and specialty material suppliers, as the technical requirements for innovative raw materials become ever more challenging
Boost blade manufacturing productivity with PU thanks to its:
- Lower viscosity, faster infusion speed
- Faster curing, improved productivity
- Reduced exothermic activity
Achieve superior performance with PU for:
- Lighter, stronger and longer blades
- Excellent mechanical performance
- Superior fatigue resistance
- Superior interface with glass fabric