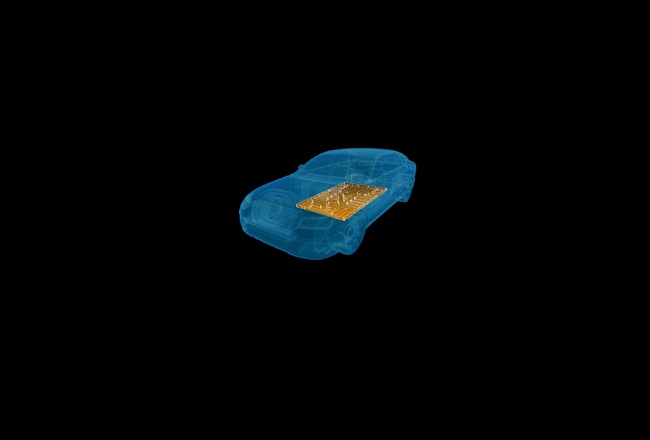
故事
聚氨酯材料和粘合剂可提高 EV 电池的碰撞安全性和动力
电动汽车日益受到大众的欢迎,但出于对续航里程和充电时间的顾虑,尤其是担心电池在发生事故时存在火灾隐患,阻碍了电动汽车的进一步普及。我们采用聚氨酯基材料、粘合剂和拉挤成型技术,打造一款可大幅提高碰撞安全性的电池组。
创新材料是克服电动汽车发展瓶颈的关键
在二氧化碳减排目标、政府法规以及公众对气候变化的普遍担忧等因素推动下,预计未来几年道路上的电动汽车 (EV) 数量将会激增。但许多消费者对电池驱动汽车和插电式混合动力汽车仍心存疑虑,担心续驶里程和充电时间过长问题,尤其担心在发生碰撞时电池的安全性。为尽快从内燃机模式转型,汽车制造商、电机组件供应商和电动汽车电池制造商需要能够解决这些难题的创新材料。
科思创提出的全新 EV 电池组概念将能战胜这一挑战。这个全新 EV 电池组概念中结合了我们的 Baydur® PUL 拉挤成型技术,可制造坚固且具有碰撞安全性的外壳;与此同时,在导热缝隙填料和粘合剂中使用 Desmodur® 和 Desmophen® 作为热界面材料 (TIM),提高电池性能。
适用于具有成本效益的复合电池外壳的拉挤成型技术
汽车制造商需要使用一些模块化、轻质且坚固的电池框架,能够在有限空间中尽可能多地封装锂离子电池,但与传统材料相比,仍可保持极强的坚固可靠性。
我们采用成熟的拉挤成型工艺,采用耐用聚氨酯树脂和玻璃纤维或碳纤维制作复合框架零件。通过回火拉挤模具拉出连续纤维,同时注入液态聚氨酯。然后将材料成型并硬化,随后再切割成所需的形状和尺寸。上述流程可通过单一且具有成本效益的制造工艺,生产出坚固轻质的电池外壳。
基于 Desmodur® 和 Desmophen® 的粘合剂和缝隙填料,可提高电池的导热性,让电池更安全且功能更强大。
在多次碰撞模拟测试中,科思创解决方案的性能始终优于基准材料
我们将以拉挤成型聚氨酯制作的系列电池安装在底板、支柱和框架中,对电池外壳设计进行测试。在两次关键模拟测试中,我们的 Baydur® PUL 解决方案的性能均优于常规基准电池组:一次是根据中国标准的碰撞测试,一次是根据 NCAP 要求进行侧杆碰撞测试。模拟实验检测了电池组的能量吸收和变形情况,结果表明,科思创设计方案可大幅降低电池损坏的可能性。此外,在三项评估机械完整性、机械冲击和振动性能的 UNECE R100 测试中,科思创电池设计取得了卓越的性能结果。
导热界面材料可提高电池速度并缩短充电时间
在电池外壳中,间隙填充物和粘合材料存在的意义是为改善从电芯到冷却设备的热传递。更好的热传递意味着更好的电池性能。与传统的氧化铝基金属相比,集成了我们 德士模都® 和 Desmophen® 聚氨酯产品的 TIM 更轻便、更导热,为电动汽车提供了更大的动力和更快的充电速度。它们还将过热的电芯彼此隔离,从而降低着火的风险。
这款创新电池组不仅能够提供碰撞安全性,在碰撞测试中表现出的性能显著优于基准材料,同时具有轻质和模块化的特性。
关键优势
- 坚固和可靠 在碰撞测试中,电池组表现的性能显著优于基准外壳材料。
- 轻质 聚氨酯基材料比氧化铝外壳金属更轻。
- 提高安全性 碰撞导致电池变形的可能性较小。
- 成本效益 拉挤成型是一种适合制作耐用复合零件的成熟制造工艺。
- 模块化 拉挤成型板可通过模块化的方式,应用于大小型电池组。