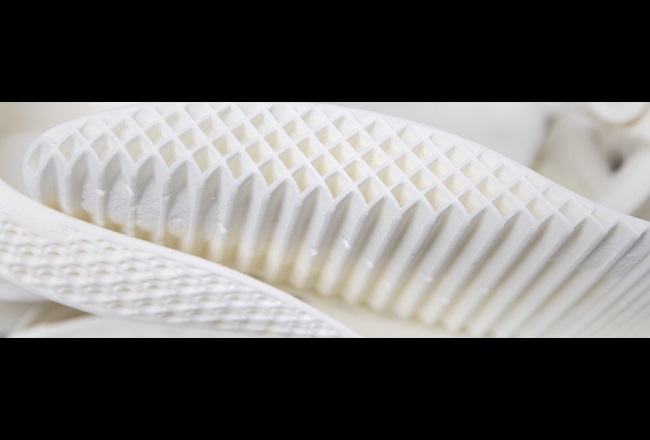
Story
Our versatile polymers toolkit for industrial AM
Additive manufacturing (AM) is a rapidly growing, agile market – and the current trend toward industrialization could bring far-reaching benefits. At Covestro, we are supporting high-precision, sustainable AM techniques with our versatile polymers toolkit and cross-cutting industry expertise.
Innovative benefits of additive manufacturing
Innovative 3D printing provides some unexpected hindsight into centuries of manufacturing techniques which, despite their many differences, all added value by subtracting material. 3D printing or additive manufacturing takes the opposite approach and creates a new object, layer by layer, starting from scratch. Instead of relying on a complex machine park, production is radically simplified thanks to one very powerful machine: the 3D printer.
These universal systems give businesses the means to decentralize their manufacturing operations. Efficient on-demand production near the point of sale makes it possible to reduce inventories and energy consumption by transporting fewer intermediates and finished products.
As for the development and production phases, product designers gain the ability to achieve complex geometries using fewer parts and manufacturers no longer need expensive molds required in injection molding and other processes. Add in easily programmable revisions and endless customization potential, and it is quickly apparent that the value of additive manufacturing lies in both the product and the process.
Innovative 3D printing provides some unexpected hindsight into centuries of manufacturing techniques which, despite their many differences, all added value by subtracting material. 3D printing or additive manufacturing takes the opposite approach and creates a new object, layer by layer, starting from scratch. Instead of relying on a complex machine park, production is radically simplified thanks to one very powerful machine: the 3D printer.
These universal systems give businesses the means to decentralize their manufacturing operations. Efficient on-demand production near the point of sale makes it possible to reduce inventories and energy consumption by transporting fewer intermediates and finished products.
As for the development and production phases, product designers gain the ability to achieve complex geometries using fewer parts and manufacturers no longer need expensive molds required in injection molding and other processes. Add in easily programmable revisions and endless customization potential, and it is quickly apparent that the value of additive manufacturing lies in both the product and the process.
Tacking industrial challenges with the right printable materials
Until recently, the multiple benefits of 3D printing applied mostly to pre-production processes. 3D printed prototypes still offer a quick and affordable way to test-drive a tool or design before investing in costly production equipment.
But the new era of additive manufacturing is no longer concerned solely with hypotheticals. Instead, manufacturers are looking to apply the technology in real-world industrial applications. Mass production poses a whole new set of requirements over design prototypes. One of the biggest challenges is getting the right materials.
At this stage of the game, the materials available in the 3D printing market are often not suitable for functional parts. Manufacturers need more versatile solutions with variable properties such as enhanced flexibility or toughness. That is where the specialists at Covestro are rising to the challenge and supporting OEMs with materials, expertise and integrated insights to leverage the great potential of additive manufacturing. Lukas Breuers, Marketing Manager at Covestro, explains, “As a leading supplier of high-tech polymers, our goal is to bring manufacturers in multiple industries one big step closer to producing different products on the same machine, on demand and anywhere around the world.”
Until recently, the multiple benefits of 3D printing applied mostly to pre-production processes. 3D printed prototypes still offer a quick and affordable way to test-drive a tool or design before investing in costly production equipment.
But the new era of additive manufacturing is no longer concerned solely with hypotheticals. Instead, manufacturers are looking to apply the technology in real-world industrial applications. Mass production poses a whole new set of requirements over design prototypes. One of the biggest challenges is getting the right materials.
At this stage of the game, the materials available in the 3D printing market are often not suitable for functional parts. Manufacturers need more versatile solutions with variable properties such as enhanced flexibility or toughness. That is where the specialists at Covestro are rising to the challenge and supporting OEMs with materials, expertise and integrated insights to leverage the great potential of additive manufacturing. Lukas Breuers, Marketing Manager at Covestro, explains, “As a leading supplier of high-tech polymers, our goal is to bring manufacturers in multiple industries one big step closer to producing different products on the same machine, on demand and anywhere around the world.”
Just as 3D printing is revolutionizing many industries, new trends and technologies are shaping the world of 3D printing. One of the most exciting trends is industrialization. Thanks to recent developments, 3D printing is starting to shed its reputation as a pre-production technology. No longer just a tool for rapid, affordable prototyping, the growing set of layering techniques known as additive manufacturing (AM) is quickly evolving into a full-blown industrial production technology – with enormous potential for manufacturers and consumers as well as the environment.
As a leading supplier of high-tech polymers, our goal is to bring manufacturers in multiple industries one big step closer to producing different products on the same machine, on demand and anywhere around the world.
How Covestro is improving 3D printing techniques
At Covestro, we supply materials for all major technologies in the field of additive manufacturing. Our versatile polyurethane and polycarbonate building blocks, as well as many other polymers, offer our customers a flexible toolkit for 3D printable materials. They can be tuned to the requirements of specific applications to support a multitude of desired properties such as hardness, resilience, heat and chemical resistance, and flexibility.
Our printable materials offer manufacturers and designers in various industries unmatched freedom in terms of functionality, complexity, and design. We also offer a growing portfolio of bio-based and CO2-based polymers that contribute to vital sustainability goals and reduce the environmental impact of production.
Fused filament fabrication (FFF)
Fused filament fabrication is the most common AM process. It relies on a continuous stream of filament material which is fed into a heated printer head and extruded onto a build platform. FFF is suitable for numerous different industries, from the rapid prototyping of musical instruments or driver controls to the production of medical products such as prostheses using biocompatible polymers.
We offer a wide range of extrudable raw materials for FFF, from high-strength polycarbonate (PC) and its blends to flexible thermoplastic polyurethanes (TPU). The latter are available with a wide property portfolio, including hardness values that range from Shore A 70 to Shore D 74. Both PC and TPU support a broad range of application temperatures from low-temperature flexible TPU grades used in products like ski boots to high-temperature APEC PC grades for applications in excess of 150°C. For applications requiring a high flame retardancy, PC is an ideal choice.
Powder bed fusion
Powder bed fusion is an AM technique that uses energy from a laser beam to fuse particles of powder into a solid form. The powder bed gradually exposes layer upon layer to the laser beam until an object is formed. Powder bed fusion is used in numerous industries, from aerospace to medical to the footwear industry. It has been used to print aircraft part prototypes, dental retainers and customized midsoles. A similar powder-based 3D printing technique is high-speed sintering (HSS). In the HSS process, an infrared-light absorbing ink is applied to a powder layer, which is then exposed to irradiation from an infrared lamp.
For powder bed fusion processes, we offer thermoplastic polyurethane (TPU) powders which are available with a wide range of properties. They offer durable elasticity, a snappy response and good resistance to tearing and abrasion. Additional benefits include compatibility with a low build area temperature, adjustable melting behavior and high recycling rates.
Stereolithography (SLA) and Digital Light Processing (DLP)
Stereolithography and digital light processing are two similar AM techniques that start with a liquid photopolymer which is then selectively cured and solidified through exposure to a laser beam (SLA) or a projector or arc lamp (DLP). SLA has been used for medical modelling in applications such as reconstructive head, oral and maxillofacial surgery. DLP has been used to create print patterns for investment casting as well as high-detail applications such as dental, jewelry and art.
Our tailor-made polyurethane resin systems for SLA and DLP offer unique, customizable performance. Their mechanical properties can be adjusted over a wide range from flexible to incredibly tough. Our prepolymers for liquid resins are highly resistant to shrinkage and offer an outstanding resistance to chemicals and weathering. They also offer color-fast properties and can be formulated in a wide range of colored or transparent grades.
At Covestro, we supply materials for all major technologies in the field of additive manufacturing. Our versatile polyurethane and polycarbonate building blocks, as well as many other polymers, offer our customers a flexible toolkit for 3D printable materials. They can be tuned to the requirements of specific applications to support a multitude of desired properties such as hardness, resilience, heat and chemical resistance, and flexibility.
Our printable materials offer manufacturers and designers in various industries unmatched freedom in terms of functionality, complexity, and design. We also offer a growing portfolio of bio-based and CO2-based polymers that contribute to vital sustainability goals and reduce the environmental impact of production.
Fused filament fabrication (FFF)
Fused filament fabrication is the most common AM process. It relies on a continuous stream of filament material which is fed into a heated printer head and extruded onto a build platform. FFF is suitable for numerous different industries, from the rapid prototyping of musical instruments or driver controls to the production of medical products such as prostheses using biocompatible polymers.
We offer a wide range of extrudable raw materials for FFF, from high-strength polycarbonate (PC) and its blends to flexible thermoplastic polyurethanes (TPU). The latter are available with a wide property portfolio, including hardness values that range from Shore A 70 to Shore D 74. Both PC and TPU support a broad range of application temperatures from low-temperature flexible TPU grades used in products like ski boots to high-temperature APEC PC grades for applications in excess of 150°C. For applications requiring a high flame retardancy, PC is an ideal choice.
Powder bed fusion
Powder bed fusion is an AM technique that uses energy from a laser beam to fuse particles of powder into a solid form. The powder bed gradually exposes layer upon layer to the laser beam until an object is formed. Powder bed fusion is used in numerous industries, from aerospace to medical to the footwear industry. It has been used to print aircraft part prototypes, dental retainers and customized midsoles. A similar powder-based 3D printing technique is high-speed sintering (HSS). In the HSS process, an infrared-light absorbing ink is applied to a powder layer, which is then exposed to irradiation from an infrared lamp.
For powder bed fusion processes, we offer thermoplastic polyurethane (TPU) powders which are available with a wide range of properties. They offer durable elasticity, a snappy response and good resistance to tearing and abrasion. Additional benefits include compatibility with a low build area temperature, adjustable melting behavior and high recycling rates.
Stereolithography (SLA) and Digital Light Processing (DLP)
Stereolithography and digital light processing are two similar AM techniques that start with a liquid photopolymer which is then selectively cured and solidified through exposure to a laser beam (SLA) or a projector or arc lamp (DLP). SLA has been used for medical modelling in applications such as reconstructive head, oral and maxillofacial surgery. DLP has been used to create print patterns for investment casting as well as high-detail applications such as dental, jewelry and art.
Our tailor-made polyurethane resin systems for SLA and DLP offer unique, customizable performance. Their mechanical properties can be adjusted over a wide range from flexible to incredibly tough. Our prepolymers for liquid resins are highly resistant to shrinkage and offer an outstanding resistance to chemicals and weathering. They also offer color-fast properties and can be formulated in a wide range of colored or transparent grades.
Adopting a holistic approach toward industrial AM
Beyond our industry expertise and tunable materials, we also collaborate with machine manufacturers to optimize both hardware and our polymer materials for high-speed processes. Our comprehensive approach addresses relevant challenges on the road to industrial AM, so that more sustainable and individual production may soon become a viable, widespread reality.
Beyond our industry expertise and tunable materials, we also collaborate with machine manufacturers to optimize both hardware and our polymer materials for high-speed processes. Our comprehensive approach addresses relevant challenges on the road to industrial AM, so that more sustainable and individual production may soon become a viable, widespread reality.