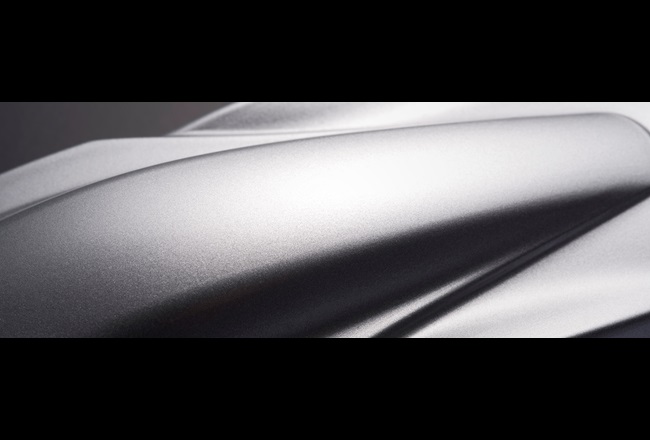
Technologie
Nachbearbeitung von Kunststoffen: Mehrwert für Bauteile und Baugruppen
Nach ihrer Herstellung müssen Kunststoffteile unter Umständen auf irgendeine Art und Weise zusammengefügt werden, ob durch mechanische Verbindungselemente, Verkleben, Schnappverbindungen, Verschweißen oder andere Fügetechniken. Zur Erzielung des gewünschten Endergebnisses müssen die Kunststoffteile ggf. auch noch lackiert, beschichtet oder metallisiert werden.
Mit einer durchdachten Bauteilgestaltung kann das Zusammenfügen optimiert werden: Gut konstruierte Teile verfügen über Merkmale, die eine korrekte Positionierung und Ausrichtung gewährleisten. Eine aktive Verbesserung der Teilemontage führt häufig zu Kosten- und Zeiteinsparungen. Eine Methode ist das Spritzgießen von Teilen, die benötigte Beschläge überflüssig machen oder reduzieren. Die Beseitigung mechanischer Verbindungselemente, wie Schrauben und Bolzen, senkt die Montage- und Zerlegungskosten. Oft können mechanische Verbindungselemente unter anderem durch Schnappverbindungen und Riegel ersetzt werden. Die Fabrikation beeinträchtigt Ästhetik und Funktionalität eines Teils. Dekorative Effekte lassen sich durch Lackierung und Laserbeschriftung erzielen. Lackier-, Beschichtungs- und Metallisierungsverfahren werten die Ästhetik auf und verleihen Teilen, die aus verschiedenen Werkstoffen bestehen oder mit unterschiedlichen Verfahren hergestellt wurden, eine einheitliche Farbe und Textur. Darüber hinaus bieten bestimmte Lacke noch zusätzliche Funktionen, wie zum Beispiel Leitlacke zur EMV-Abschirmung. Manche Teile müssen ggf. auch maschinell bearbeitet oder anderen Endbearbeitungsvorgängen unterzogen werden, um die gewünschte Optik zu erhalten.
Fügen von Kunststoffteilen: Eine Auswahl an Verfahren
Für die Fertigung eines komplexen Teils müssen manchmal zwei oder mehr Komponenten zusammengefügt werden. Eine Reihe von Fügeverfahren bietet kosteneffiziente, ästhetisch ansprechende und mechanisch solide Lösungen für die Konstruktion und Herstellung aufwendiger Bauteile. Das verwendete Fügeverfahren richtet sich nach der erforderlichen Festigkeit des Endprodukts und danach, ob die Komponenten zerlegbar sein müssen. Zu den Fügeverfahren gehören unter anderem:
• Kleben – Das Kleben bezieht sich auf die Verbindung mit Lösemitteln oder Klebstoffen. Klebstoffe halten Komponenten durch das Auftragen einer Oberflächenschicht zusammen, die beide Flächen chemisch miteinander verbindet, wohingegen Lösungsmittel die Oberflächen chemisch aufweichen und dann verdunsten, um die Verbindung zu schaffen.
• Schnappverbindung – Diese häufig eingesetzte Methode ist eine einfache, wirtschaftliche und effiziente Option für das Zusammenfügen von Kunststoffteilen. Schnappverschlüsse werden in die Geometrie der Formteile eingeplant und ermöglichen eine einfache Demontage.
• Schweißen – Beim Verschweißen thermoplastischer Teile werden die zu verschweißenden Oberflächen durch Hitze aufgeweicht. Während des Wiedererstarrens wird der Kontakt zwischen ihnen aufrechterhalten. Die Methoden zur Zuführung der Wärmeenergie unterscheiden sich von Verfahren zu Verfahren.
• Mechanische Verbindungselemente – Mechanische Verbindungselemente, einschließlich Schrauben, Bolzen und Gewindeeinsätzen, gehören zu den zuverlässigsten und gebräuchlichsten Fügeverfahren, insbesondere bei Geräten, die für Wartungszwecke wiederholt zerlegt werden müssen.
• Kleben – Das Kleben bezieht sich auf die Verbindung mit Lösemitteln oder Klebstoffen. Klebstoffe halten Komponenten durch das Auftragen einer Oberflächenschicht zusammen, die beide Flächen chemisch miteinander verbindet, wohingegen Lösungsmittel die Oberflächen chemisch aufweichen und dann verdunsten, um die Verbindung zu schaffen.
• Schnappverbindung – Diese häufig eingesetzte Methode ist eine einfache, wirtschaftliche und effiziente Option für das Zusammenfügen von Kunststoffteilen. Schnappverschlüsse werden in die Geometrie der Formteile eingeplant und ermöglichen eine einfache Demontage.
• Schweißen – Beim Verschweißen thermoplastischer Teile werden die zu verschweißenden Oberflächen durch Hitze aufgeweicht. Während des Wiedererstarrens wird der Kontakt zwischen ihnen aufrechterhalten. Die Methoden zur Zuführung der Wärmeenergie unterscheiden sich von Verfahren zu Verfahren.
• Mechanische Verbindungselemente – Mechanische Verbindungselemente, einschließlich Schrauben, Bolzen und Gewindeeinsätzen, gehören zu den zuverlässigsten und gebräuchlichsten Fügeverfahren, insbesondere bei Geräten, die für Wartungszwecke wiederholt zerlegt werden müssen.
Metallisieren, Lackieren und Drucken: Eine Welt voller Möglichkeiten
Durch Metallisieren, Lackieren und Bedrucken können Sie Teile vor Chemikalien oder UV-Strahlen schützen, elektronische Geräte vor elektromagnetischer Strahlung abschirmen oder grafische Elemente hinzufügen. Mit diesen Verfahren können Hersteller die Ästhetik ihrer Teile aufwerten und Produkten, die aus verschiedenen Werkstoffen bestehen oder mit unterschiedlichen Verfahren hergestellt wurden, eine einheitliche Farbe und Textur verleihen.
• Metallisieren – Beim Metallisierungsverfahren werden metallische Beschichtungen auf Polycarbonatteile aufgetragen. Durch dekorative metallische Beschichtungen können thermoplastische Teile als wirtschaftliche, leichtgewichtige Alternativen zu Metallen dienen, während funktionale metallische Beschichtungen EMV-Abschirmung, Leiterbahnen oder reflektierende Oberflächen ermöglichen. Metallische Beschichtungen können durch Galvanisieren, stromloses Metallisieren, Vakuummetallisierung und Sputter-Beschichtung aufgetragen werden.
• Lackieren – Durch Lackierungen können Spritzgussfehler kaschiert werden, sie bieten eine breite Palette an Farben und Oberflächeneffekten und schützen Kunststoffe vor Chemikalien, Abrieb oder Umwelteinflüssen. Darüber hinaus erfüllen einige Lacke auch zusätzliche Funktionen, wie zum Beispiel Leitlacke zur EMV-Abschirmung.
• Bedrucken – Wird häufig zum Auftragen von Designs, Buchstaben und Beschriftungen auf thermoplastische Teile verwendet. Es gibt mehrere verschiedene Druckverfahren, darunter Tampondruck, Siebdruck, Sublimationsdruck, Laserdruck und Heißprägung. Zur Dekoration bestimmter Teiletypen oder -formen bieten sich unterschiedliche Verfahren an. Der Siebdruck ist beispielsweise ein kostengünstiges Verfahren zum Dekorieren flacher oder zylindrischer Kunststoffteile. Beim Sublimationsdruck wird das tiefe Eindringen der Tinte genutzt, um abriebfeste Drucksymbole auf haltbaren Kunststoffteilen wie Computertastaturen zu erzeugen.
Wenn Dekore bereits während der Verarbeitung und nicht im Rahmen eines sekundären Prozesses nach dem Herstellungsprozess aufgetragen werden, können Kosteneinsparungen bei der Dekoration erzielt werden. Einige Verfahren der In-Mold-Decoration bieten Optionen, die mit einer herkömmlichen Lackierung nicht umsetzbar wären, zum Beispiel mehrfarbige Grafiken und Muster.
• Metallisieren – Beim Metallisierungsverfahren werden metallische Beschichtungen auf Polycarbonatteile aufgetragen. Durch dekorative metallische Beschichtungen können thermoplastische Teile als wirtschaftliche, leichtgewichtige Alternativen zu Metallen dienen, während funktionale metallische Beschichtungen EMV-Abschirmung, Leiterbahnen oder reflektierende Oberflächen ermöglichen. Metallische Beschichtungen können durch Galvanisieren, stromloses Metallisieren, Vakuummetallisierung und Sputter-Beschichtung aufgetragen werden.
• Lackieren – Durch Lackierungen können Spritzgussfehler kaschiert werden, sie bieten eine breite Palette an Farben und Oberflächeneffekten und schützen Kunststoffe vor Chemikalien, Abrieb oder Umwelteinflüssen. Darüber hinaus erfüllen einige Lacke auch zusätzliche Funktionen, wie zum Beispiel Leitlacke zur EMV-Abschirmung.
• Bedrucken – Wird häufig zum Auftragen von Designs, Buchstaben und Beschriftungen auf thermoplastische Teile verwendet. Es gibt mehrere verschiedene Druckverfahren, darunter Tampondruck, Siebdruck, Sublimationsdruck, Laserdruck und Heißprägung. Zur Dekoration bestimmter Teiletypen oder -formen bieten sich unterschiedliche Verfahren an. Der Siebdruck ist beispielsweise ein kostengünstiges Verfahren zum Dekorieren flacher oder zylindrischer Kunststoffteile. Beim Sublimationsdruck wird das tiefe Eindringen der Tinte genutzt, um abriebfeste Drucksymbole auf haltbaren Kunststoffteilen wie Computertastaturen zu erzeugen.
Wenn Dekore bereits während der Verarbeitung und nicht im Rahmen eines sekundären Prozesses nach dem Herstellungsprozess aufgetragen werden, können Kosteneinsparungen bei der Dekoration erzielt werden. Einige Verfahren der In-Mold-Decoration bieten Optionen, die mit einer herkömmlichen Lackierung nicht umsetzbar wären, zum Beispiel mehrfarbige Grafiken und Muster.
Maschinelle Bearbeitung & Endbearbeitung: Der letzte Schliff
Die maschinelle Bearbeitung und Endbearbeitung kommt gelegentlich zum Einsatz, um Formteilen das gewünschte Aussehen oder eine zusätzliche, für die Montage benötigte Funktionalität zu verleihen. Diese Arbeitsgänge werden üblicherweise eher für die Fertigung von Prototypen und zum Abgraten oder Modifizieren von Teilen genutzt, die durch Thermoformen oder Extrusion hergestellt wurden. Spritzgussteile müssen selten weiterbearbeitet werden. Die Bearbeitung umfasst unterschiedliche subtraktive Verfahren, bei denen ein Schneidwerkzeug unerwünschtes Material von einem Teil entfernt, um die gewünschte Form zu erhalten. Die maschinelle Bearbeitung von Kunststoffteilen kann bei der Herstellung großer Mengen teuer werden, kommt jedoch häufig als Nachbearbeitungsverfahren zum Einsatz, bei dem kleinste Materialmengen entfernt werden und die Zykluszeit kurz ist. Die gebräuchlichsten maschinellen Bearbeitungsverfahren sind unter anderem:
• Bohren & Aufreiben – Werden am häufigsten zur Herstellung von Löchern in Teilen verwendet.
• Fräsen – Wird eingesetzt, um mit hoher Genauigkeit und Präzision große Mengen des thermoplastischen Werkstoffs zu entfernen.
• Drehen – Wird oft zur Herstellung runder Formen verwendet.
Das Tempern ist ein wichtiger Schritt, der nicht bei allen Bauteilen erforderlich ist, aber bei der Reduzierung von Spannungen und der Erhöhung der Stabilität der Bauteile nach der Bearbeitung hilft. Thermoplastische Komponenten, die ohne vorheriges Tempern poliert werden, können bei der Benutzung reißen.
Endbearbeitungsverfahren, einschließlich Polieren oder Glanzschleifen, können zur Reparatur von Abrieb oder versehentlichen Oberflächenkratzern, zur Fertigbearbeitung von Bohrlöchern und Kanten von Polycarbonatteilen und zur Erzeugung der gewünschten Oberflächenerscheinung oder -textur eingesetzt werden. Es ist wichtig, vor der Auswahl eines Endbearbeitungsverfahrens auf die wärmebeständigen Eigenschaften des Werkstoffs zu achten.
Wir bieten Herstellern technische Unterstützung im Hinblick auf die maschinelle Nach- und Endbearbeitung von Polycarbonatteilen.
• Bohren & Aufreiben – Werden am häufigsten zur Herstellung von Löchern in Teilen verwendet.
• Fräsen – Wird eingesetzt, um mit hoher Genauigkeit und Präzision große Mengen des thermoplastischen Werkstoffs zu entfernen.
• Drehen – Wird oft zur Herstellung runder Formen verwendet.
Das Tempern ist ein wichtiger Schritt, der nicht bei allen Bauteilen erforderlich ist, aber bei der Reduzierung von Spannungen und der Erhöhung der Stabilität der Bauteile nach der Bearbeitung hilft. Thermoplastische Komponenten, die ohne vorheriges Tempern poliert werden, können bei der Benutzung reißen.
Endbearbeitungsverfahren, einschließlich Polieren oder Glanzschleifen, können zur Reparatur von Abrieb oder versehentlichen Oberflächenkratzern, zur Fertigbearbeitung von Bohrlöchern und Kanten von Polycarbonatteilen und zur Erzeugung der gewünschten Oberflächenerscheinung oder -textur eingesetzt werden. Es ist wichtig, vor der Auswahl eines Endbearbeitungsverfahrens auf die wärmebeständigen Eigenschaften des Werkstoffs zu achten.
Wir bieten Herstellern technische Unterstützung im Hinblick auf die maschinelle Nach- und Endbearbeitung von Polycarbonatteilen.