
故事
Bayfill® 发泡模拟技术为模具和生产工艺设计提供强有力的支持
汽车设计日益数字化。我们最新的模拟软件可以预测被Bayfill® 聚氨酯泡沫填充的仪表板的发泡过程和材料特性。凭借这项数字孪生技术,可提前识别生产过程中的风险和问题,避免发现问题后对产品进行修改处理导致成本增加。
数字化技术:加速汽车设计阶段,缩短开发周期
对一辆新车进行数字化建模是汽车设计阶段的核心。新车建模的规模远不止简单地对其结构和形式进行模拟。汽车制造商需要利用材料建模科学为全新的产品设计建立数字孪生模型,模拟从仪表盘、仪表板到内饰的各种部件。
汽车主机厂及其零件厂商通常会对特定零件要求数字验证,并利用材料模型中获得的信息来确认如何遵照规定的要求进行零件模拟行为。这最大限度地减少了后期的工艺设置或生产阶段对物理试验的需求以及可能产生的错误,同时减少了资源使用。通过模拟来进行验证,可缩短开发周期,降低产品复杂性,同时可规避风险以及产品不确定性的发生。这个方法可以帮助汽车主机厂及其零件厂商降低成本,为早期设计阶段提供更多决策支持。
卓越的高质量软质触感仪表板发泡解决方案:Bayfill®
我们的半硬质聚氨酯 (PU) 模塑泡沫 Bayfill® 经常用于汽车内饰,比如软质触感的仪表板和内饰等零部件。它的工艺流动非常好,可以经济可靠得生产一些轮廓精确的复杂零件。
Bayfill® 还以其舒适的触感和降噪性能,为汽车内饰设计提供了自由度。特殊的泡沫配方也可用于具有增强碰撞性能的安全零件。
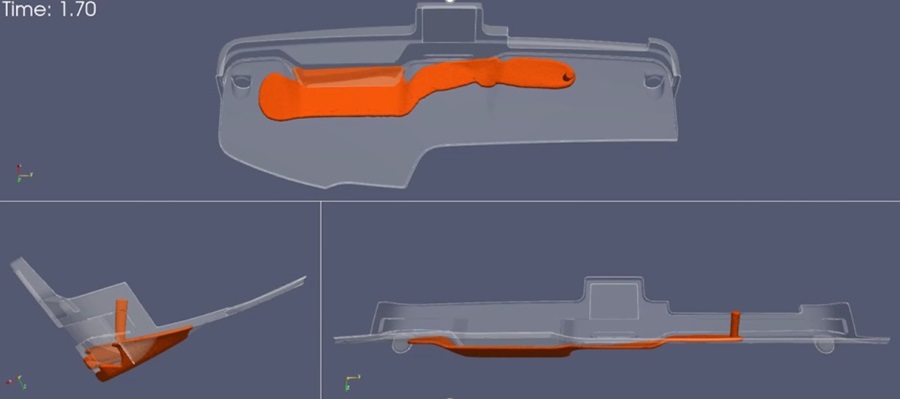
Bayfill® 发泡过程模拟可帮助尽早确定最适合的模具设计和工艺设置。
我们采用了自主研发的材料模型,并将它们与强大的计算能力相结合,来打造符合未来发泡工艺的数字孪生模型。该孪生模型可以反映发泡过程,为零件厂商在对产品进行任何必要试验或试错采样之前提供材料加工方面的详细信息,还可在设计阶段就预测生产过程中的不确定性。如在设计阶段对产品或模具做修改,成本也较低。。我们已成功为一个系列的仪表板模拟软件完成了首次测试和验证。目前,科思创可以利用其创新的模拟技术帮助完成仪表盘发泡过程的第一次数字验证。这个过程需要客户提供最终的高质量 CAD 模型,包括主要载体、泡沫以及外壳。此外,科思创与客户密切合作,以作出具有现实意义的假设,确保得到更精确和有意义的模拟结果。
采用聚氨酯泡沫有助于实现仪表板所需的性能,但必须在一定时间范围内完成发泡,并进行正确设置。基于我们自主研发的材料模型,模拟环境中的 Bayfill® 发泡过程精准地模拟了虚拟环境中的材料特性,有助于校准最佳的加工窗口。将有助于在虚拟加工环境中精准地模拟材料特性。
我们先进的发泡过程模拟软件可为客户带来很多切实的好处。提前验证材料加工行为和仪表板设计可在设计阶段之前发现和解决潜在问题,进而避免在完成加工设置后因修改产品带来的高昂金钱和时间成本。另外,减少设置试验的次数也可节省能源和资源的使用。减少发泡模具的潜在返工次数,也可降低模具制造商来回运输的成本,同时减少能源的使用和材料的损耗。在某些情况下,该模拟软件还可避免生产多余的发泡原型模具。这些都是标准的仪表板模具。
当我们创建用于 Bayfill® 发泡过程模拟的数字孪生模型时,零件厂商和汽车制造商即可获得详细的材料加工信息。发泡模具和产品设计均可在早期设计阶段进行优化,此时如需修改产品和模具,成本相对比较合理。在设计早期完成强有力的模具设计和工艺设置,可在关键的产品发布阶段节省宝贵的时间和降低成本。
8B9P6apZCTTLTmkNsB3_GE
https://asset-out-cdn.video-cdn.net/private/videos/8B9P6apZCTTLTmkNsB3_GE/thumbnails/1221727?quality=thumbnail&__token__=exp=1757245860~acl=/private/videos/8B9P6apZCTTLTmkNsB3_GE/thumbnails/1221727*~hmac=d27629e9ab980e2c8721636fd8016fde95d747a01947a365399cff838a7b12d8
Bayfill Foaming Simulations.mp4
我们采用自主研发的 PU 材料模型和最新的软件为 Bayfill® 仪表板发泡过程创造了数字孪生模型。 这样一来,汽车零件厂商和汽车制造商均可在早期设计阶段清楚地透视整个材料加工过程,进而得到更强大的发泡模具和更高效的工艺设计。
关键优势
- 早期信息: 发泡过程模拟可帮助客户在早期设计阶段作出正确决策。
- 全面性: 材料建模发泡加工过程创建了完整的数字孪生模型。
- 规避风险: 材料特性和发泡过程的验证可提前避免生产过程中的问题。
- 降低成本: 可减少客户在发泡过程中的试验、模具以及密封工作的不断返工。
- 优化工艺流程: 该模拟可帮助客户使用最少的材料完成有效的设置。
- 工艺见解: 验证泡沫注入位置或路径、模具温度、空气滞留和排气布局。
- 节省时间: 数字验证帮助客户在早期设计阶段做出正确决策。
- 降低复杂性: 该模拟过程可以提高设计决策过程的确定性。