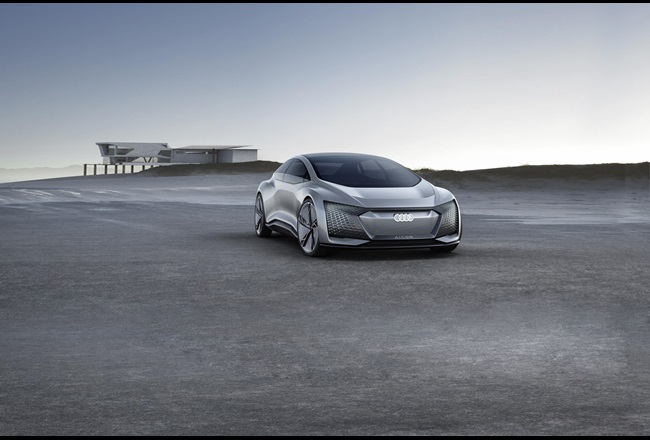
故事
节能的 Blulogiq® 清漆工艺可实现高质量的汽车表面
科思创的 Blulogiq® 是一种创新的潜伏性固化剂解决方案,帮助汽车原始设备制造商及其供应商提高涂料工艺的能效。减少固化时间和温度可降低二氧化碳足迹,而不会影响表面光洁度或耐用性。
汽车原始设备制造商在聚氨酯表面涂层方面需要对能源效率进行权衡
随着轻量化塑料车身部件和保险杠等塑料悬挂组件变得越来越普遍,汽车制造商及其供应商面临着如何使聚氨酯 (PU) 清漆喷涂工艺更省时、更节能的难题。
典型溶剂型、未催化涂层工艺的优点是在流平过程中交联缓慢,从而确保了良好的流平性和外观。另一方面,烘干机中的硬化速度也十分缓慢,因此烘烤需要更长时间。随后,部件仍需要更多的时间和空间进行烘箱后固化,才能在不损坏表面质量的情况下进行处理或加工。
将我们的 Desmodur® 多异氰酸酯基 PU 涂料与 DBTL(二月桂酸二丁基锡)催化剂结合使用,可大大加快烘箱中的硬化速度,但同时也促进了流平过程中的早期交联,从而对涂层的外观产生负面影响。此外,在继续加工前,仍可能需要部件暂存区以进行进一步的烘干机后硬化。
Desmodur® blulogiq® 3190 清漆:在较低的烘箱温度下更快地交联
潜伏性意味着固化过程由热量触发。在流平期间,几乎没有反应,因为热潜催化剂在该温度下具有惰性。这种较高的早期抗性可形成光滑的膜,并产生高质量的表面外观。
与标准催化剂解决方案相比,在烘箱中,Desmodur® blulogiq® 3190 清漆工艺可大大加快交联速度。在 80°C 下仅需 10 分钟即可达到与 DBTL 催化的 Desmodur® 25 分钟相同的硬化水平。更快的固化速度意味着从烘干机出来的部件几乎完全硬化,从而消除了对材料存储区的需求,并减少了运输损耗和报废率。与此同时,活化时间与固化速度并不相关,因为粘度仍然比催化剂解决方案低得多。
更重要的是,对于轻质的多材料车身部件,Blulogiq® 可使最高固化温度从 140°C 降至仅 90°C。结合合适的二道浆和底漆,可以在初始电沉积涂层 (EDC) 后对所有涂料层进行低温涂覆。
这为汽车行业的原始设备制造商和供应商降低了干燥机温度,缩短了烘烤时间或两者结合,极大地提高了能源效率,并减少了聚氨酯涂料工艺的二氧化碳排放量。
无需基础设施投资或牺牲表面外观即可提高生产率
我们的 Blulogiq® 清漆解决方案将在金属和塑料材料的溶剂型 2K PU Cc(双组分聚氨酯清漆)涂料工艺中为供应商和汽车原始设备制造商赋予先发优势。
对于以超过 30 欧元的成本制造悬挂式塑料汽车保险杠的供应商,通过使用Blulogiq® 工艺,由于缩短了周期时间,减少使用或直接取缔了存储区,从而为其节省高达 6% 的成本 。 ,并且事实证明,其干燥后的处理也更快捷和简单。供应商可以更早地对部件进行抛光,运输更方便省事,且运输中的损坏也更少。这些改进都可在不牺牲光学质量的前提下实现。
汽车原始设备制造商无需任何新的基础设备投资,就可以选择从新流程中获得最大利益。90°C的低温涂装线可大大提高能效,减少碳足迹,为制造商实现自己的二氧化碳减排目标铺平了道路。
制造商可以继续使用传统的 140°C 工艺,来提高生产率以降低单位成本,或选择以较慢的升温来改善表面外观——甚至在装配新涂装车间时将干燥箱的长度减少多达 20%。对于带有大槛板的电动汽车,高温工艺中的整体烘烤稳健性也很重要。
我们的 Blulogiq® 涂料工艺通过降低能源成本,减少二氧化碳排放以及部件报废率而提高可持续性。目前,这种新颖的清漆解决方案已在两家汽车制造商的生产线终端维修中使用,一些原始设备制造商的首条生产线试验也已完成。
我们新颖的 Blulogiq® 热潜固化剂工艺解决了汽车涂料中的多个问题。原始设备制造商可以降低烘箱温度以提高能效并减少碳足迹,或提高高温涂装生产线的生产率。它为 2K PU 涂层系统带来了按需固化的可能性。
关键优势
- 低温固化 原始设备制造商和供应商可将涂料干燥机的温度从 140°C 降至 90°C。
- 减少二氧化碳足迹 更快的固化和更低的烘箱温度降低了能耗和排放。
- 节约成本 得益于更快的干燥和处理,最多可为悬挂式塑料零件节省 6% 的成本。
- 高温效率 在 140°C 的涂装线上提高产量或缩短烘箱长度。
- 即用型解决方案 Blulogiq® 清漆工艺不需要投资于新的基础设施。