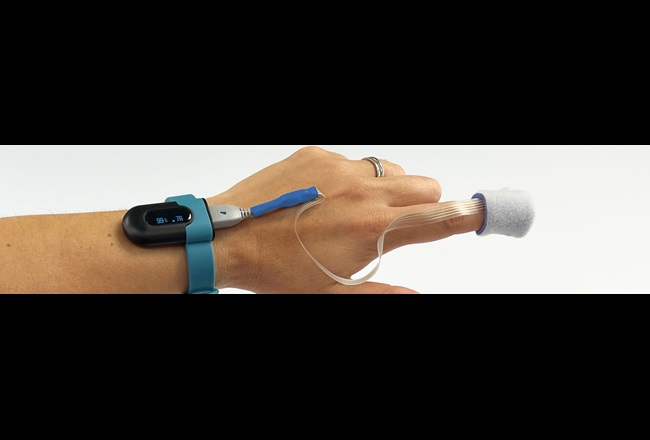
Platilon® TPU 薄膜助力高性能医疗可穿戴设备
柔性印刷电子产品:医疗可穿戴设备的关键
由于许多国家/地区的人口老龄化,医疗可穿戴设备市场正在迅速增长。这些“随身设备”中的柔性电子设备允许实时远程跟踪佩戴者的生命体征。这样可以及早发现健康问题并促进预防医学。与传统的刚性传感器不同,新一代医疗可穿戴设备配备了柔性电路。它们重量轻、延展性好且佩戴舒适。
热塑性聚氨酯薄膜因其特性而成为创新医疗保健应用的理想选择。我们的 Platilon® TPU 薄膜不仅具有良好的成型性、柔软的质地和较高的佩戴舒适度,而且还专为集成柔性印刷电子产品而设计。这使它们成为用于患者监测的柔性可穿戴设备的合适基材。
脉搏血氧仪表明 Platilon® TPU 薄膜是印刷电子产品的最佳基材
为了突出 TPU 薄膜在医疗可穿戴设备中的有效性,我们在北美的特殊薄膜医疗团队与 SunRay Scientific Inc. 合作,SunRay Scientific Inc. 是一家为柔性印刷电子产品制造商提供无铅导电油墨、环氧树脂和粘合剂的领先供应商。
我们共同开发了一款功能齐全的脉搏血氧仪,能够监测生物信号和血氧饱和度 (SpO2)。在这个项目中,Platilon® TPU 薄膜用作印刷电路和医疗传感器的基材。这个设备演示了我们的特殊薄膜不仅满足所有功能要求,而且还能够顺利集成到现有的制造工艺中。
我们为什么一起开发这款血氧仪设备?
新一代智能、灵活的皮肤贴片取代了远程患者监测中的刚性电子元件。这些新型医疗设备需要印刷有导电层的基板,以适应复杂的电路设计、电极和生物传感器。嵌入在人体传感器中的电子设备必须在佩戴者移动时完美运行,并提供不会刺激或损伤皮肤的生物相容性。科思创和 SunRay Scientific 联合开发了这款设备,以展示 TPU 薄膜如何使这些类型的医疗传感器无缝集成到现有制造工艺中。
这个心率传感器和血氧仪是如何制造的?
SunRay 的 StretchS 银油墨电路印刷在我们的 Platilon® TPU 薄膜上。LED 和光电传感器二极管与导电环氧树脂 ZTACH® ACE 连接,银环氧树脂用于将柔性电路连接到引线。TPU 电路连接到市售的电子控制器。由此产生的设备可以无缝监测患者的脉搏和氧气含量。
为什么 Platilon® TPU 薄膜是集成传感器和印刷电子产品的最佳基材?
TPU 薄膜是电子组件中柔性电路的最佳选择,因为它们可以在可拉伸导电层中容纳电路设计,同时还集成了各种生物传感器技术,包括光电传感器、电极和脉冲传感器。同时,TPU 具有固有的柔韧性、抗撕裂性和抗穿刺性,以及生物相容性和穿着舒适度,同时还可以作为出色的空气和液体屏障。Platilon® TPU 薄膜可以通过加热或超声波密封,使其成为可穿戴传感器等健康应用的绝佳选择。
Platilon® TPU 薄膜在医疗可穿戴设备中的优势
与传统的刚性和非可拉伸基材相比,可拉伸和柔性印刷电子产品在健康和医疗可穿戴设备中具有显著优势。我们的 Platilon® TPU 薄膜产品组合支持需要适应各种体型和功能的随身可穿戴设备。它们的高成型性和轻质、亲肤柔软性确保了患者的舒适度,提高了依从性并增强了健康问题的早期识别。Platilon® TPU 薄膜可实现印刷电子产品的无缝和隐蔽集成,同时还为佩戴者提供生物相容性和舒适性。
关键词
- 灵活: TPU 薄膜是用于印刷电路、传感器和电极的柔性基材。
- 无缝: 轻质、亲肤的 TPU 薄膜可无缝融入医疗可穿戴设备。
- 弹性: TPU 薄膜可以适应穿着者的体型和动作。
- 生物相容性: TPU 薄膜对皮肤温和、柔软且透气。