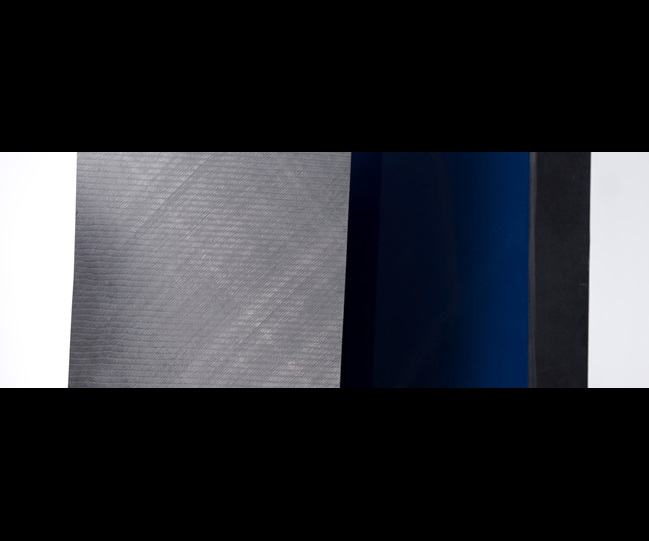
Polyurethane made for carbon in cars
Our Baydur® matrix system: The key to safer and more efficient cars
To meet the needs of automakers and to push forward the possibilities within the automotive sector, we have developed a Baydur® matrix system for carbon fiber structural components in cars.
Carbon-fiber-reinforced polyurethane (PUR) composites offer huge potential for reducing vehicle weight and, thus, CO2 emissions. Our Baydur® matrix system has three times the energy-absorption potential of comparable resins. It is therefore able to provide an extremely high level of occupant safety in the event of a collision. Automakers and direct suppliers also benefit from high productivity because the components are manufactured efficiently using the state-of-the-art high-pressure resin transfer molding (HP-RTM) process.
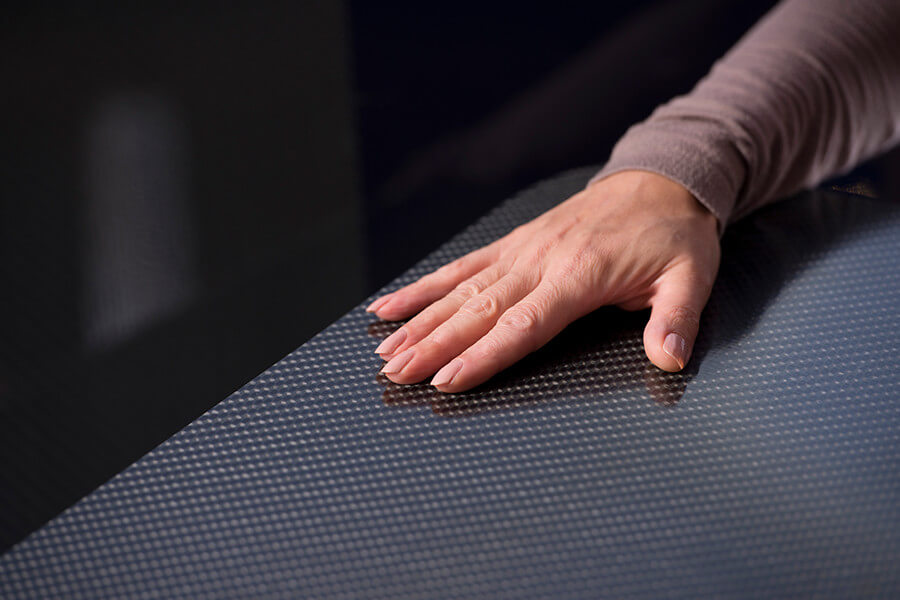
Innovative production for high-end results
The HP-RTM process has proved very effective for manufacturing robust composite parts in volumes in the low hundreds of thousands. Wovens or fabrics with oriented carbon fibers are first laid in the open mold, which is then closed. In the space of a few seconds, the low-viscosity PU system is injected into the closed mold under high pressure. Thanks to the high reactivity of the PU system, the composite cures rapidly and fully (snap cure) and the component can be demolded and processed after a short time. Cycle times are just a few minutes, with consistently high quality thanks to the lower temperature in the mold.
Benefits of Baydur® matrix system in a nutshell
- Three times higher energy-absorption potential compared to other resins
- Lightweight material reduces CO2 emissions
- High-level occupant safety in the event of an accident
- Efficient HP-RTM manufacturing process