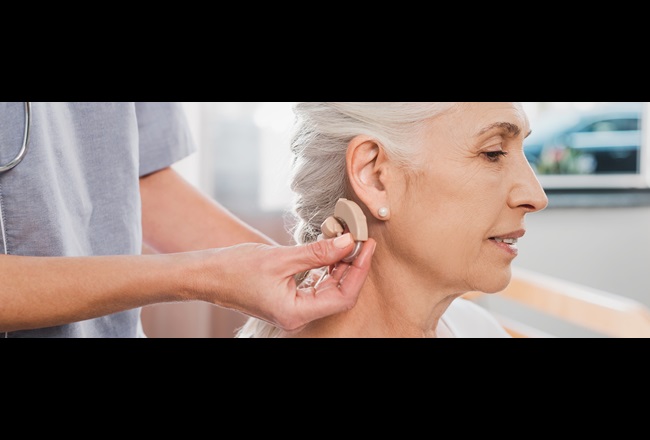
Customizable materials for 3D printed hearing aids
The process of printing unique hearing aids for every ear
Additive manufacturing is used to produce soft earmolds for behind-the-ear (BTE) devices as well as hard shells for in-the-ear (ITE) designs. While the electronics for BTE products are located in a casing behind the ear, ITE hearing aids integrate them within the design.
These two basic types of hearing aids both require ear impressions, which are taken by inserting impression material into the outer ear or the ear cavity. These impressions are sent to a lab, where they are scanned, modelled and finally used to create the plastic components for 3D printed hearing aids.
For the printing process, manufacturers often rely on an additive manufacturing technique known as digital light processing (DLP). During DLP, liquid photopolymers are exposed, layer by layer, to a light beam. The energy from the laser cures the photopolymer and builds earmolds or shells from scratch. Soft earmolds are ready to be integrated in BTE devices. Hard shells are outfitted with electronic components and then sealed. After the products undergo quality testing, the tailor-made hearing aids are ready to be shipped to hearing healthcare professionals who fit them on the device users.
Benefits of 3D printed hearing aids: Comfort, performance, efficiency
Like other additive manufacturing techniques, DLP is well-equipped to handle complex geometries, including internal cavities, even for very small objects. This inherent design freedom lets hearing aid manufacturers create devices that are perfectly tailored to the contours of every ear. The process is also efficient, as several unique earmolds or shells can be built on a single tray during the same process.
Printed hearing aids ensure a higher degree of comfort for patients as well as fewer fit issues and subsequent adjustments for audiologists. Achieving an accurate fit is especially important for designs that are worn all day inside the ear. Here, comfort goes hand in hand with performance: because customized hearing aids provide a better fit, they also contribute to an improved auditory experience. Most importantly, sound does not leak from the receiver inside the ear back into the microphone (the ear’s window to the outside world), a phenomenon known as acoustic feedback. A good fit also prevents whistling and other unpleasant effects.
Beyond comfort and function, however, another essential requirement for hearing aids is durability: in the end, a perfect fit is only perfect for the lifetime of the device.
Challenges for hearing aid manufacturers: Combining comfort and durability
Hearing aids need to perform in a challenging environment and withstand a wide variety of factors – inside the ear and out. They are exposed to moisture in the ear, i.e. sebum and cerumen, as well as other environmental factors.
Certain chemicals found in cleaning agents can also eat away at the devices. In hard shells, they can cause holes which impact the device’s performance (e.g. whistling) and shorten its useful life.
For hearing aid manufacturers, addressing these challenges often boils down to the choosing the right materials for maximum, lasting performance. Materials that address comfort, durability and chemical resistance can help manufacturers go the extra mile so that end consumers can get more out of their devices.
To ensure the best possible fit, every hearing aid has to be customized, formerly a long process that depended on the expertise and dexterity of trained professionals. Today, the manufacturing process for hearing aids is far less labor-intensive and far more automated.
For the current generation of hearing healthcare professionals, achieving an accurate fit goes hand in hand with advanced technologies. Because every piece is unique and tailored to the customer’s ear, custom hearing aids are the perfect application for 3D printing. Indeed, additive manufacturing techniques have won over large portions of the industry and millions of hearing aids are 3D printed each year.
Because of the variability of their basic building blocks, polyurethane-based resins offer the unique opportunity to achieve customize performance for properties such as toughness, flexibility, and chemical resistance. With our tailor-made materials, we can support hearing aid manufacturers in achieving key properties such as resistance to sweat, cosmetics, sunscreen and UV rays.
Customizable polyurethane resins from Covestro for high-performance 3D printed hearing aids
For the high demands of 3D printed medical applications such as hearing aids, superior quality polyurethane-based resins present an ideal solution.
Thomas Büsgen, Head of Technical Development Additive Manufacturing at Covestro explains, “Because of the variability of their basic building blocks, polyurethane-based resins offer the unique opportunity to achieve customized performance for properties such as toughness, flexibility, and chemical resistance. With our tailor-made materials, we can support hearing aid manufacturers in achieving key properties such as resistance to sweat, cosmetics and sunscreen.”
Covestro’s biocompatible polyurethane-based systems provide lightweight comfort. Depending on the type of device, they can be tuned to offer the right degree of hardness or softness to maximize comfort for both BTE and ITE products. Polyurethane-based systems also offer excellent resistance to harsh chemicals used for cleaning. Their toughness enables low wall thicknesses, making it possible to safely hide ITEs deeper inside the ear. Moreover, the water vapor permeability of polyurethane shells, a familiar feature in PU-based textile coatings, improves moisture control in the ear canal.
The photopolymers may be customized and designed to meet the diverse requirements of hearing aid manufacturers – with tunable, individual properties to address most medical application requirements.
Would you like to find out more? Get more information about our PU-based resins or request a sample.