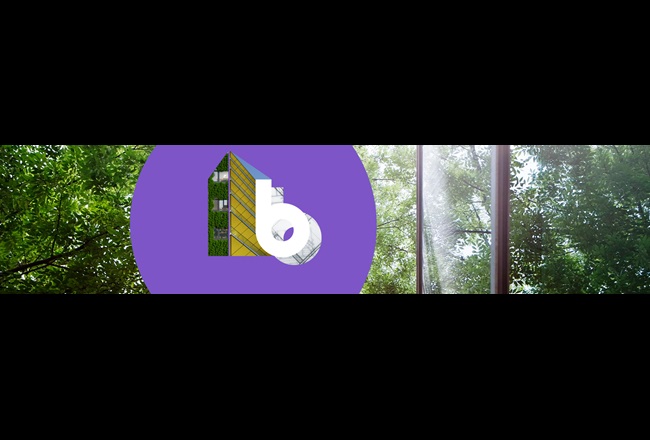
Pioneering circular solutions to transform the building and construction sector
Mechanical Recycling: Transforming waste into valuable resources
Recycling is a crucial factor for achieving a circular and low-carbon construction. Mechanical recycling of PU foams is a significant step forward in this direction and it is already existing today.Through this process, companies collect and process end-of-life rigid Polyurethane foam insulation boards, transforming them into new, high-quality boards. The approach promotes reuse of materials, reducing the need for virgin resources, and cutting down on waste generation.
In simpler terms, PU foams are collected, shredded into smaller pieces, and processed to make new boards, all while maintaining the foam's original quality to provide a durable new material.
Our trusted partner, Puren, plays a vital role in advancing this innovative process, turning recycled PU materials into durable, high-performance insulation boards.
Chemical Recycling: Innovative solutions for a more sustainable future
While mechanical recycling is a significant step forward, we are also pioneering chemical recycling through the EU-funded Circular Foam project1. This collaborative initiative, involving 22 partners from nine EU countries, aims to achieve full circularity for PU rigid foams. Chemical recycling processes, such as chemolysis and smart pyrolysis, break down used PU foams into their molecular components. These components can then be used to make new PU foam with the same high quality as the original.
With the Circular Foam project, we're making significant strides in chemical recycling for rigid polyurethane foam, moving us closer to our vision of full circularity.
Our commitment to sustainable innovation
We are dedicated to sustainability and innovation. By using both mechanical and chemical recycling, we aim to set new standards in the construction sector. Our goal is to reduce waste, lower emissions2, and create a circular economy model that can be replicated across Europe and beyond.
As leaders in the Circular Foam project, we work with top universities and industry partners to develop these recycling processes. Together, we are making the construction industry more sustainable and ready for future challenges.
1 Circular Foam (circular-foam.eu)
2 Emissions reduction based on internal LCA calculations stages A1-A3 (cradle-to-gate) according to the EN15804+A2 standard using a mass balance approach.
Curious? Check out the FAQs!
How do end-of-life raw materials get back to you?
This varies from region to region. We work in partnership with waste collection companies to find the best solutions.
How does Covestro's "Circular Foam" project aim to improve the chemical recycling of rigid foams?
The project aims to develop a feasible and scalable solution, transforming PU rigid foam back into chemicals that can be converted again into foams, keeping the same properties from the fossil-based version.
What advancements in recycling technologies are being made to enhance the circularity of PU rigid foam?
Through the Circular Foam project, Covestro, together with its partners, is testing different alternatives for chemical recycling to find a feasible solution to transform end-of-life PU rigid foams back into foams while maintaining the same performance.
Have you already built recycling plants at Covestro sites?
Covestro is already running a pilot facility for recycling of PU flexible foams and is currently working to find a solution for end-of-life for PU rigid foams, through the Circular Foam project.
Which partners do you collaborate with to ensure effective recycling?
For the Circular Foam project, Covestro is working together with 22 partners from the PU rigid foam value chain, aiming to find a feasible solution for chemical recycling of these foams.